
aerofoils
By Chris Heintz
We have to keep in mind that the airfoil of our flying surfaces
is only one variable of the many components which makes our airplanes fly well -
or not so well - in a range of possible configurations. When we do an
investigation of any part of our aircraft we must not look at this part as THE
solution, rather we must always remember that it is only one part of a whole.
Analysis is necessary; but only a synthetic view will give us the whole picture.
It is a bit like somebody trying to understand the human body by studying the
skeleton only, or the chemicals of the body only, etc.: the failure of modern
medicine comes from this fact. Scientists look at the parts of a corpse and
decide they know something about a living body!
But, let us go back to something less serious (!?!) and look at
the airfoil or wing section of our airplane in such a way that we will have a
little better understanding of how our aircraft flies.
Relative Motion
Today it is universally accepted that an airfoil in motion
through still air and air blowing over a stationary airfoil have the same
effects. This was not the case in scientific circles some 120 years ago, but now
is common knowledge, and justifies the wind tunnel tests where true air flows
over an airfoil and from which we can predict characteristics of an airplane
moving through still air. The important thing is the relative speed of airfoil
and air.
Reynolds Numbers Early
investigations into the theory of fluid dynamics have predicted a certain number
of constants to which similar disturbances (and an airfoil in the air is a
disturbance) produce similar effects - in hydrodynamics, these are referred to
as 'Froude Numbers" (hulls of boats); in high speed aerodynamics the "Mach
Number' are other examples. For our smaller and slower aircraft, the only
"number" which really needs to be considered is the "Reynolds Number" and it is
defined as:
Re = V x I /
v
Where: V = Relative speed (m/sec) I =
typical "length" of a solid body (M) v = cinematic viscosity of the
air (sec/m2)
Re is a dimensionless number, which
makes it independent of the measuring systems. The cinematic viscosity is to a
certain extent dependent on the density of the air, but for our aircraft flying
below 12,000 ft., it can be assumed constant (equivalent to 15 x 106
sec/m2 in metric).
The speed can easily be converted to metric: 1 mph = 1.15
Kts. = 1.61 km/h = 1.61 / 3.6 m/s = .45 m/sec.
The same applies to the length:
1 ft. = .305 m.
Our small aircraft have a wing chord, which is the "length" to
use when talking about airfoils, of some 5 ft. equivalent to 1.5 m.
Thus the Reynolds number simplifies to:
Re = (.45 x vmph x 1.5) / (15 x
10-6) = 4.5
vmph
or at stall speed of 50 mph: Re = 1.8 x
106 (you know that 106
= 1,000,000 = 1 million).
Keep in mind the above values are for a 5 ft. chord. For a
2-1/2 ft. chord typical of tail surfaces or the tip of a tapered wing, the
Re will be only 1/2 above values.
If the air is looked at, not as a continuous medium, but
composed of small balls (the molecules of modern physics), there is obviously an
average distance between those balls. The Reynolds number is then nothing else
than the relation between the typical solid body length to this average distance
between the molecules of the air in which the solid is moving.
As long as this Reynolds number is between the values of .4 x
106 (400,000) and some 10 X 106 (ten million) what we will
say about airfoils will apply.
Note that for smaller Re (say 10,000 to 400,000, which
is the range for radio controlled models and smaller windmills), other lows
apply; however, we will not consider these numbers in this present set of
articles which deal with light planes. The same applies at very large Reynolds
numbers, which are practically associated with Mach numbers larger than .3,
where the compressibility of the air can no longer be neglected as it is in
classic aerodynamics which considers the air as an incompressible, continuous
medium.
Boundary Layer
When the air hits the airfoil leading edge it will separate
into the upper and lower airstream, which meets again at the trailing edge. (See
Figure 1).

It is obvious that the air very close to the airfoil "rubs"
against the solid surface and is slowed down. In other words, starting
downstream of the impact point, the air loses some of its momentum, or velocity.
And it loses more and more as we follow it along the path close to the solid
airfoil. We can see that friction creates an area where there is less speed. The
reduced speed area just outside of the airfoil becomes thicker and thicker as we
follow it from the leading edge to the trailing edge. This area is called the
boundary layer. Its thickness is increasing as described and is defined
as the thickness at which the local free stream speed is finally reached. (See
Figure 2). A typical boundary layer thickness is 1/2" near the trailing edge.
The friction, which obviously, is a loss, results in the friction drag of the
airfoil.
Again the theory of fluid dynamics shows that there are two
possible types of stable boundary layers:
The first, to build up, is called 'laminar" because the flow is
nice and steady and the friction drag is relatively low.
The second is called 'turbulent" because the flow is rather
rough and the friction drag is higher.
The unfortunate thing is that the "laminar boundary layer" will
automatically become turbulent (with associated higher drag) close to the
leading edge of the airfoil unless very special precautions are taken. These
precautions are:
A very smooth airfoil surface: Slight construction defects (or
bugs as they stick to the airfoil leading edge) will change the laminar boundary
layer into a turbulent one. Unless you have a perfect airfoil and keep it
this way forget about the gain possible with a laminar flow!
A special shape of the airfoil: The pressure distribution on
the airfoil is related to the airfoil shape. Today we can calculate (with high
speed computers) airfoils which maximize the length of the laminar boundary
layer. Still, what is mentioned in a) applies. But, do not get desperate. The
friction drag of the airfoil with a laminar boundary layer is .08, whereas in
turbulent flow it becomes .12. Sure, this is a 50% increase but only on the
friction drag of the airfoil. The other drag contributions are airfoil shape,
wind induced drag, tail drag, fuselage and landing gear drag, interference drag,
cooling drag and a few more. Your aircraft will never go 50% faster just by
changing the airfoil - at the very best, you may gain a few (3 to 5) percentage
points.
Airfoil Design and Geometry
I will simply refer you to a very good (and understandable)
book, Theory of Wing Sections by Ira Abbott and Albert Von
Doenhoff (Dover, 1959), available as a reprint from EAA. Get your copy and study
it a bit.
Part 2
In part 1, we discussed the significance of relative motion,
Reynolds numbers and the Boundary Layer (laminar or turbulent). And there was
some homework on basic airfoil design and geometry so that the reader should now
be familiar with chord, leading edge. trailing edge, mean line curvature,
thickness etc., as shown in Figure 1.
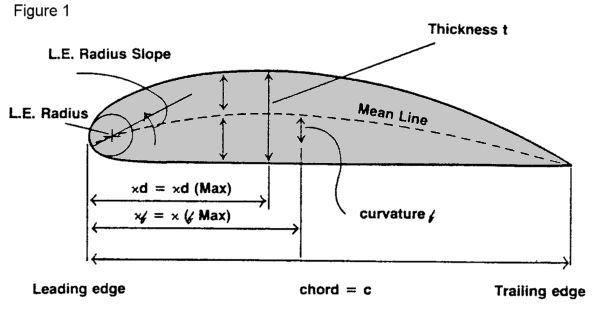
As this discussion is limited to airfoils used on light planes,
we will ask ourselves: What are the most significant features we would like to
achieve with our airfoils?
-
We want to fly as quickly as possible (short take-off), thus
need high lift at low speed.
-
We want to have full control of the aircraft as soon
as airborne and throughout the whole speed range.
-
For a given thrust (engine horsepower, intake, exhaust and
propeller) we want a high cruise speed, thus need low drag at high
speed.
-
In all configurations we want a strong airframe without
undue weight - thus we need a thick airfoil to be able to use a deep
spar and have a large "torque tube" which will give bending strength and
stiffness as well as torsional strength and rigidity.
-
We also want good climb characteristics which means high
lift and low drag in the climb attitude - with good engine cooling and a
light airframe to be able to use full power and climb at slow speed with a
high rate of climb (steep climb).
As already obvious from the above listing. there will be some
compromising in the selection of the airfoil - but the airfoil is only one
parameter. Others are wing planform (rectangular, tapered, etc.), wing tips,
wing twist (we will discuss this topic, as it seems to be one that is frequently
misunderstood or underestimated), wing aspect ratio, or span loading (which
seems to be overestimated).
Over the years, it is very interesting to follow the designs of
aircraft that are popular - there is a fashion in aircraft just as there is in
clothing - pants, long skirts. mini skirts - racy looking aircraft, old fashion
classics. new looks, etc.
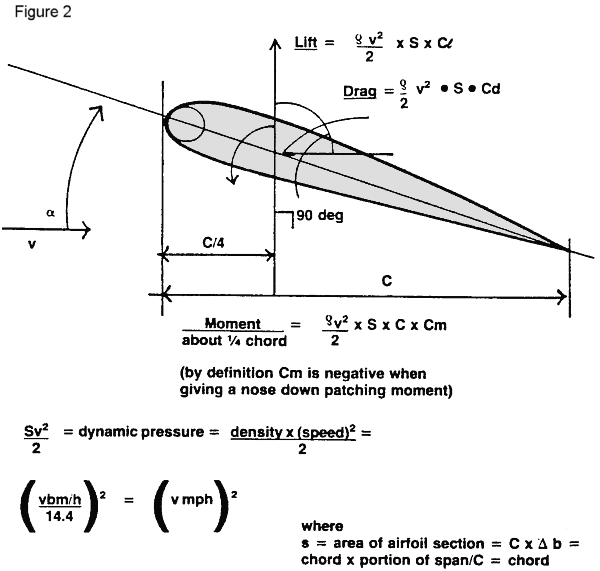
The Force on an Airfoil
But let
us look today at following basic airfoil requirements and later on see how we
have to design the wing so that the same requirements can be further improved
upon (or at least not lost!).
We'll consider:
With classic airfoils, those used over the last 30 to 50 years,
we have accustomed to a maximum lift coefficient of 1.4 to 1.5 with a 12 to 15%
thick (d/e) airfoil and a drag coefficient of .01 in cruise configuration (ie.
NACA 4412, NACA 22012 and NACA 23012 or 23015). All of these airfoils are
relatively insensitive to roughness (dirt or manufacturing imperfection) on the
leading edge and except for the 4412 or 4415, their moment coefficient is
relatively low so that the wing is not submitted to very large torsion at high
speed (large Sv2/2 - see forces on an airfoil).
To increase the maximum lift, traditionally an appreciable
increase in the camber is quite effective. Practically, this is done by
deflecting the rear part the airfoil with so-called flaps (or ailerons, elevator
or rudder).
It is also known that this substantial curvature increase is
associated with a large Cm equivalent to .067 S flap (deg.) To avoid designing
the whole aircraft for this condition the designer limits the "flap out" speed
(VF) to a reasonable useful range.
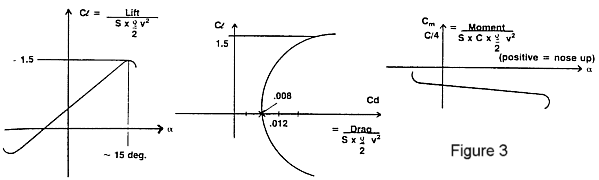
Unless relatively complicated to build, when flaps (see next
paragraph) are used, the increase in lift is moderate: to a CLMAX =
2.2, at Sf equivalent to 15 degrees. (This is a profile value - the whole wing
which usually has only 1/2 span with flaps, has a CLMAX equivalent
1.9) and because the flaps are stalled on the upper surface (because the
airstream has not enough momentum to overcome a sharp change of direction - due
to an already thick boundary layer), the drag increase becomes quite substantial
with Sf larger than 15 degrees and there is no improvement in the climb speed
range.
This drawback of the "plain" flap is partially overcome with
the more sophisticated "Fowler" flap, where a gap is created in such a way that,
when deflected, air from underneath is caught in a "funnel," accelerated and
"blown" into the boundary layer at the upper surface, thus allowing the airflow
to follow the flap contour to deflections up to 25 degrees
approximate.
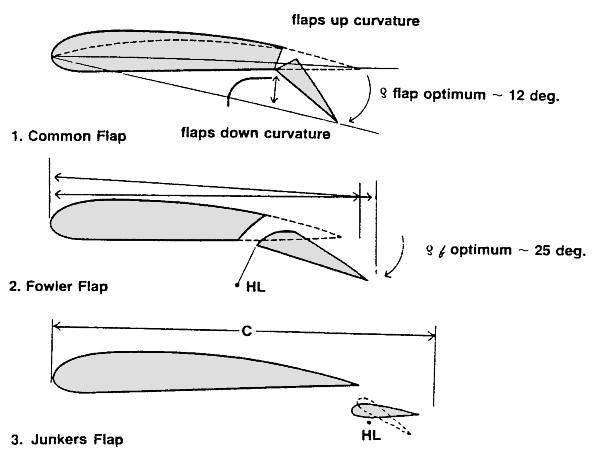
Usually the Fowler flaps are not only deflected but also moved
rearwards ( with a hinge point situated below the airfoil or a sophisticated
track system as on the Cessna 152 and 172, etc.), which increases the wing area
S by increasing the chord.
When homebuilders install this kind of flaps it is very
important that they stick to the designer's geometry because the flap nose
position with respect to the wing rear end is very critical to obtain maximum
profile lift coefficient of up to 2.6 (see NACA Rep. No. 664 - 1939)
Split flaps, although quite effective, have fallen out of
fashion and will not be discussed further [though I have re-introduced them with
the ZENITH CH 2000].
A very interesting flap is the "Junker" type. It is a separate
small airfoil under the wing trailing edge and hinged in such a way as to always
create the "funnel effect" to reactivate the upper surface
boundary-layer.
The Junker flap is especially interesting when used as ailerons
(the ailerons are flap sections on the outboard wing panels, one being deflected
down, the other up, so that the pilot has "roll control" over the aircraft.) As
already mentioned the usual boundary layer is quite thick over the rear part of
the airfoil and the ailerons need a certain minimum deflection to be effective.
This is usually small "ineffective" roll control deflection from its neutral
position. With the Junker type aileron, this is not the case if full advantage
of the possible "funnel effect" is achieved by careful design of the
hinge point location and careful construction.
The drawback of this flap is that at high speed the funnel is
always consuming some energy so that the drag coefficient is slightly higher
than for a conventional flap.
But the 'Junker' flap is a very good compromise when excellent
low speed in aileron controllability is desired, associated with high lift/low
drag in climb configuration, and the top speed end is not so important. [That is
why I chose the Junker flaperon for my STOL CH 701 design].
The 'Junker' flap always, and the 'Fowler' flap when extended,
provide a certain 'boundary layer' control, be cause they 'trim" this layer out
by blowing accelerated air into it, thus allowing the airflow to adhere to the
solid airfoil up to substantial deflections (30 to 45 degrees) without local
stalling of the airflow.
Part 3
In Part 1 of this series, we introduced our discussion of
airfoils with a study of relative flow, Reynolds numbers, boundary layers and
airfoil geometry, in Part 2, we took a look at the forces acting on an airfoil -
lift, drag and moment and some of the trailing edge devices used to increase
lift without too much penalty in drag, moment and/or building complication. In
this third part, we will try to get a better understanding of the leading edge
high lift devices, boundary layer control and stall.
To get our discussion started, let's ask this question: why
do we get the behaviour shown in Figure 1; ie., why does the lift increase when
we lower the flaps and increase further when we cut leading edge
slots?
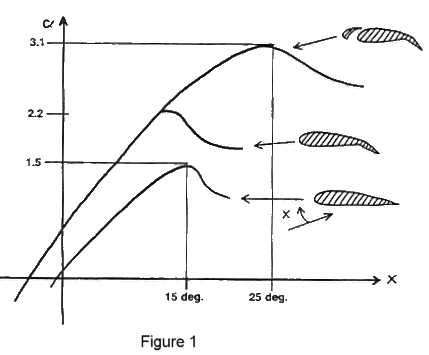
In changing from a plain airfoil to an airfoil with flaps we
have created an increase of curvature of the airfoil which gives part of the
extra lift, but we have also created a depression, a low pressure near the
trailing edge, which sucks the air over the upper part of the airfoil and helps
it to overcome the centrifugal forces present when the air flow has to come
around the nose of the wing. It is like a pull acting from the trailing edge and
pulling the air around the leading edge, thus preventing separation (see Figure
2).
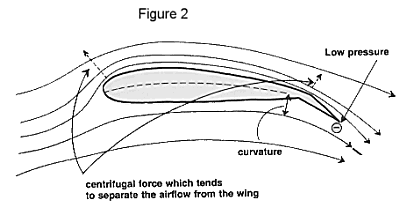
It is obvious that by slowly increasing the angle of attack
"x", there is a limit beyond which the centrifugal forces, either near the
leading edge or close to the flap hinge point, can no longer be overcome by the
trailing edge suction and the airfoil flies in separated air; in other words, is
stalled and supplies a lower lift (see Figure 1 again).
In order to be able to further increase the lift by delaying
the stall to even higher angles of attack, we have to limit the flap deflection
so that the stall will first occur at the leading edge and then provide a force
which neutralizes the centrifugal force. This can be done in various, more or
less practical ways:
Help the air move around the leading edge with a roller. This
is very effective (CL of up to 5), but not at all practical (see Figure
3a).
Increase the leading edge radius because the centrifugal force
is proportional to 1:R, ie. by increasing R we decrease the force wanting to
pull the air away from the airfoil (see Figure 3b). This is quite simple and an
easy, effective "add on." The sharper the original radius, the more effective
the modification will be. For example, Steve Wittman gained some 10 mph on his
"Tailwind" with a "sharp" original leading edge, whereas on a Zodiac CH-600,
which already had a blunt nose, the gain was negligible. Note that this
"drooped" nose also increases the curvature and, unless it is movable, there
will be a drag penalty in cruise (small angle of attack). Note also that this
modification alters the wing chord and as a result the center of gravity range
so be careful.
Simply create a depression where required; ie., some holes
through which the air is sucked inside the wing (see Figure 3C). This again is
not very practical.
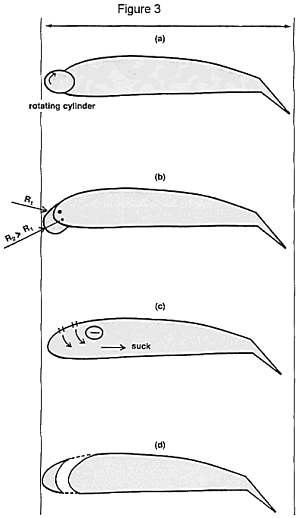
The most practical solution is to choose one area as a suction
point and build the airfoil in such a way that suction can be obtained
automatically (see Figure 3d). You know that when a given amount of air is
accelerated (its speed increases), the pressure drops. It follows that if we
guide air through a narrowing slot (a funnel) it must go faster and faster to
get through and if the exit is smaller than the entrance we have a definite
suction at the exit. So, if we cut a slot near the leading edge with a funnel
shape and further orient the exit lips so that the fast air runs out tangent to
the air foil, this will help reactivate the boundary layer and will allow us to
in crease the lift on our wing up to CL equivalent to 3 to 3.1, which is over
twice the original plain airfoil value of 1.5.
We should also keep in mind the following:
The chord is measured from leading edge to trailing edge and
the the slot is not added but the slot is cut in the airfoil; in
other words, if you add the slots to an existing wing you will alter the chord
and center of gravity to such an extent that you will also have to modify the
tall area (which will create additional stresses in the rear fuselage). You'd be
much better off to start designing a new aircraft!
The slots can also be moved further down, thus increasing
further the curvature and lift, but again this is limited by the drag increase
in cruise you feel you can live with.
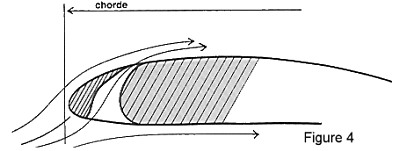
And, of course, you can retract the slots to minimize the drag
at lower angles of attack - but you have to be aware that the construction will
take longer, the aircraft will be heavier (which defeats part of the advantage)
and finally, you put an additional workload on the pilot. Let's face some facts:
on an average, we probably fly our airplanes 30 to 50 hours per year. Compare
that to driving your car one hour every weekend; you can quickly see where you
could easily become a lousy "weekend driver." If we do not want more aircraft
accidents, being the "lousy weekend flyers we are," then the machines we fly
must be pretty well adapted to what we can handle. But, this may not be the case
anymore with an additional control . . . and to make the slots retract
automatically would simply complicate the construction some more and give us
gray hair before we even fly the bird. It's a lot easier to stick with something
simple; that works without problems; that we can build in a reasonable amount of
time and enjoy flying without special skills. That's what homebuilding is all
about!
Part 4
In the last series of articles we have tried to grasp an
understanding of airfoils - the sections of the wings which keep our airplanes
airborne due to the lift provided by the airfoil geometry and the speed at which
they move through the air.
We have seen that without undue sophistication we can design
an airfoil which provides a very high lift which will allow us to fly
surprisingly slow. In other words. with a relatively small wing area and within
a given weight, we can take off and land in a very short distance because we do
not need to accelerate or decelerate to or from a high speed. We have also seen
that the proposed airfoil has a favorable lift to drag ratio at high lift; this
allows the aircraft to climb out or come in at a very steep angle allowing
following performance such as shown in figure 1.
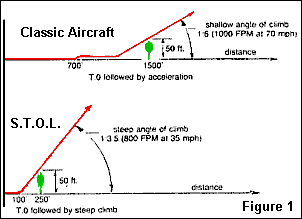
Keep in mind, however, that to obtain full advantage from the
airfoil, both flaps and slats should extend full span over the whole
wing.
The first idea will be to build one of those fantastic wings,
design a mechanism to allow full span flaperons (flaps and ailerons combined in
one full span unit and controllable as flaps with the flap control and as
ailerons with the classic aileron control through a so called "mixer") ... and
install this new wing on an existing aircraft. Although the idea sounds good,
this is too simplistic of an approach. Remember, I have already warned that the
addition of slats on any given wing will bring the aircraft "out of balance." In
the present case, although the balance will be correct, we have forgotten that the high lift is achieved at
an unusually high angle of attack (25 to 30 degrees versus the classic 15 to 18
degrees.)
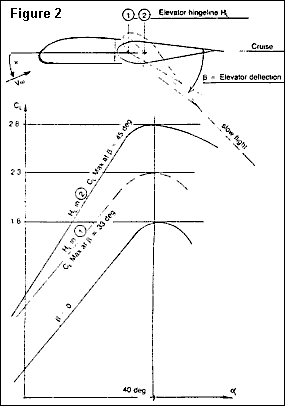
To achieve this high angle of attack, the fuselage geometry
must allow ground clearance at take off and on landing (see figure 2). From this
standpoint, a tricycle landing gear is a big plus - apart from the fact that in
normal ground position the wing has a smaller incidence with a tricycle gear
than a taildragger and will be less sensitive to high (cross) wind
taxiing.
But correct fuselage geometry is not all that is needed. Pitch
control must be able to effectively control the incidence even at the high
angles associated with slow flying. That means the horizontal tail must be able
to push the tail down in order to lift the nose up and keep the angle of
incidence high for those sustained high angle climbs.
Of course, I hear some of you talking canard, but don't forget
that the downwash behind the wing will help a classic tail - but it will have no
effect in the front!
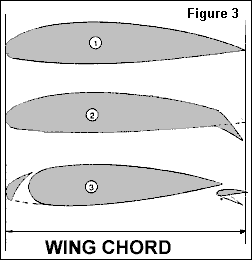
No, what we need is a horizontal tail with a high negative
lift; that is why it is "upside down." The elevator is designed to provide a
certain "funnel effect" when deflected - see figure 3. The Zenair STOL CH-701
horizontal tail has a negative maximum lift coefficient of 2.8 when the elevator
is deflected 40 degrees. But, for all this to be effective, the tail must be set
so that in cruise the drag is minimized by having the elevator in line with the
stabilator, and the whole tail airfoil at an incidence compatible with the
general airflow at this location within the downwash of the wing.
And a few more details that are important to remember when
designing a STOL aircraft are as follows:
The landing gear must be stronger than average. Human nature
being what it is, the pilot, knowing he has the ability to land in a very short
distance may take advantage of this desirable feature and "plunk" his aircraft
down in an unprepared 'pea patch,' resulting in some hard knocks for the landing
gear to absorb.
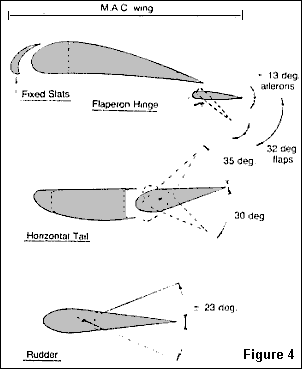
Visibility must be even better than with other aircraft designs
because of the large variations in incidence. Slow flying may bring you in the
way of faster aircraft, but remember with a STOL aircraft you are more
manoeuvrable and have an advantage to give way – see figure 4 for an
illustration of the visibility available in the STOL CH 701.
Excellent controllability at very low flying speed is absolute
necessity. Pitch control is automatically good due to the required
horizontal tail design (see again figure 3). Roll control is not bad with
full span ailerons by, again, use of the 'funnel effect' ' Instead of plain
flaperons, carefully designed "Junker" type flaperons provide excellent roll
control at low speeds without much drag penalty in cruise. (See figure
5)
Good yaw control can easily be achieved with an "all
flying rudder" (see again figure 2). This relatively large moving vertical
surface gives plenty of control in a crosswind, in the air as well as on the
ground.
And, finally, a strong airframe (6 g) is necessary so that
the pilot does not have to fear losing a wing, which might be associated with
the very light structure (430 lbs. for the Zenair STOL CH 701) used so that a
low horsepower engine (50 to 100 BHP) can be used to obtain outstanding take off
performance.
These are the trade marks of a good two-seat design.
As already discussed in a previous article, pilot comfort,
crashworthiness and an easy-to-build, long lasting airframe are simply routine
items required when designing a new generation aircraft, for which there is
apparently a need as shown by the success of the Zenair STOL CH 701.
One question which frequently crops up is: How can we
increase the cruise speed of the aircraft?
With the 65-hp Rotax 582,
the Zenair STOL CH-701 at full gross stalls at 28 mph, cruises at 74 mph (with a
top speed of 82 mph). Considering that the cruise speed is 2-1/2 times the stall
speed, this is not bad at all. Even retracting the slats would not increase the
cruise very much. The apparatus needed to make this change work are complicated
and heavy and, above all, would require an additional control. Considering the
50 or so hours most of us recreational pilots fly per year, we already have our
hands full without this additional control. It would be catastrophic to pull
"in" at the wrong time . . . and an automatic device is even more
complicated.
"Keep it simple and it works" is my motto. If you want to fly
faster, there are other good designs. For example, the two seat Zenair Zodiac
stalls at 44 mph and cruises at 105 mph, with the same horsepower as the STOL CH
701.
|