compressors
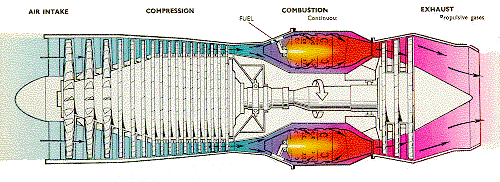
All turbine engines have a
compressor to increase the pressure of the incoming air
before it enters the combustor.
As shown in
the above figure, there are two main types of compressors:
axial and centrifugal. The compressor on the left is called an
axial compressor because the flow through the compressor
travels parallel to the axis of rotation. The compressor on
the right is called a centrifugal compressor because the flow
through this compressor is turned perpendicular to the axis of
rotation. Centrifugal compressors, which were used in the
first jet engines, are still used on small turbojets and
turboshaft engines and as pumps on rocket engines. Modern
large turbojet and turbofan engines usually use axial
compressors.
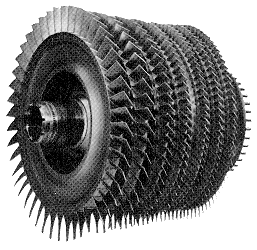
An axial flow compressor
(stators omitted for clarity). This is the high pressure
compressor from a General Electric F404 engine
Why the change
to axial compressors? An average, single-stage, centrifugal
compressor can increase the pressure by a factor of 4. A
similar single-stage axial compressor increases the pressure
by only a factor of 1.2. But it is relatively easy to link
together several stages and produce a multistage axial
compressor. In the multistage compressor, the pressure is
multiplied from row to row (8 stages at 1.2 per stage gives a
factor of 4.3). It is much more difficult to produce an
efficient multistage centrifugal compressor because the flow
has to be ducted back to the axis at each stage. Because the
flow is turned perpendicular to the axis, an engine with a
centrifugal compressor tends to be wider (greater
cross-sectional area) than a corresponding axial. This creates
additional undesirable aircraft drag. Centrifugal compressors
are also less efficient than axial compressors. For all of
these reasons, most high compression jet engines use multi
staged axial compressors. But, if only a moderate amount of
compression is required, a centrifugal compressor is much
simpler to use. |