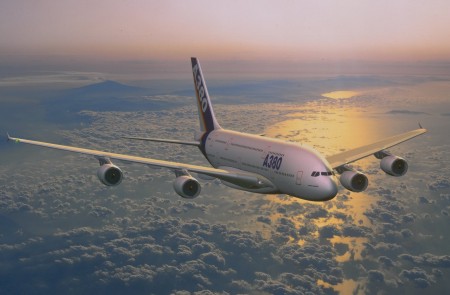
The new Airbus will
initially be sold in two versions: the A380-800, carrying 555
passengers in a three-class configuration or up to 800 passengers in a
single-class economy configuration. Expected range for the -800 model
is 8,000 nautical miles (14,800 km). The second model, the A380-800F
dedicated freighter, will carry 150 tonnes of cargo 5,600 nautical
miles (10,400 km).
The first completed
A380 at the "A380 Reveal" event in Toulouse
The first completed A380 at the "A380 Reveal" event in Toulouse. Before
starting the A380 project, both Airbus and Boeing had focused on
cornering the very-large-airliner market. Airbus and Boeing had worked
together on a study investigating a 600+ seat aircraft called the Very
Large Commercial Transport, but this cooperation did not last long.
Although both manufacturers issued various statements, the unspoken
consensus was that there was probably room for only one maker to be
profitable in the 600 to 800 seat market segment. Both knew the risk of
splitting a niche market; the simultaneous debut of the Lockheed L-1011
and the McDonnell Douglas DC-10 had demonstrated this: either aircraft
could technically fill the gap between the Douglas DC-8 and the Boeing
747, but the market could only sustain one of the two and eventually
Lockheed left the civil airliner market. However, Airbus and Boeing
decided to enter the new 600 seat market.
Boeing initially had the upper hand. The 747, though designed in the
1960s, was popular and larger than Airbus' largest jet, the A340. For
many airlines, the extra size of the 747 made it a "must buy" for their
highest density routes, and the lower costs of a common fleet led
carriers to buy additional Boeing aircraft. Boeing was considering a
New Large Aircraft to replace the 747, and acquired McDonnell Douglas
and their cancelled MD-12 design. Boeing also studied the concept of
the 747X, a version of the 747 with the forebody "hump" extended
towards the rear for more passenger room before dropping the concept.
Development of the "A3XX" began in June 1994. In 2001 it was re-branded
the A380, with the announcement of Singapore Airlines as the launch
customer.
Development
After years of research, Airbus decided to proceed with the € 8.8
billion A380 project in 1999, the final budget settling at about € 12
billion. The double-decker layout would provide higher seat capacities,
and hence cost savings, than a traditional design.
The A380's wing has been designed to cope with a Maximum Take-Off
Weight (MTOW) of 590t, albeit with some strengthening required,
allowing for a future stretch. The stronger wing (and structure) is
used on today's freighter version, the A380-800F. This approach
sacrifices some fuel efficiency on the initial passenger model but the
sheer size of the aircraft coupled with the significant advances in
technology over the years should provide lower operating costs per
passenger than the various versions of the 747. [1]
First flights
The first A380 prototype, serial number 001, was unveiled during a
ceremony in Toulouse, on January 18, 2005. It has the French
registration F-WWOW. The maiden flight took place at 8:29 UTC (10:29
a.m. local time), April 27, 2005. The prototype departed runway 32L of
Blagnac International Airport in Toulouse, France with a flight crew of
six, carrying 22 tons of flight test instrumentation and water
ballasts.
The crew consisted of French test pilots Jacques Rosay (captain for the
take-off and the initial part of the test flight) and Claude Lelaie
(captain for the second part of the test flight including the landing).
Engineers included three flight test engineers (Spanish, French, and
German), and one French test flight engineer. With the recent
Franco-German controversy over the leadership of EADS still fresh in
mind, Airbus issued a statement to make it clear that the crew had been
chosen based not on nationality but competence.
The take-off weight of the aircraft was 421 tonnes (464 US tons), or
about 75 % of its maximum take-off weight for commercial flights. This
was the heaviest take-off weight of any passenger airliner ever
created.
After take-off, the jet headed west toward the Bay of Biscay, then
south over the northern Pyrenees Mountains and concluded with a low
altitude fly-by over the town of Toulouse. The 233 minute flight
involved conducting tests on its engines, hydraulics and electronics,
while the on-board test equipment recorded measurements for 150,000
different parameters and sent data back to computers on the ground.
The A380 now faces another year of in-flight testing before formal
certification and commercial use.
On October 18, 2005, the second A380 took to the skies. The flight,
taking off and landing at Toulouse, was to test performance at cruising
height and fuel consumption of the Rolls Royce Trent 900 engines.
In November 2005 the 3rd A380 took off for the first time in Toulouse.
In mid November 2005, the A380 embarked on a tour of south-east Asia
and Australia, partly as a promotion, and partly as part of its
long-haul flight testing. The aircraft flew from Singapore to Brisbane
on the 12th, then on to Sydney on the 13th, performing a public flypast
over the harbour on its arrival. Further flights to Melbourne and a
return to Brisbane are also scheduled. The flight around Australia was
part of celebrations for Qantas's 85th anniversary. On these flights,
colours of various airlines were applied - Singapore Airlines and
Qantas - in addition to the house colours.
Cockpit
Mockup of the flight deck. Airbus made the cockpit layout, procedures
and handling characteristics similar to those of other Airbus aircraft
to reduce crew training costs. Accordingly, the A380 features an
improved glass cockpit, and fly-by-wire flight controls linked to
side-sticks.
The improved cockpit displays features eight 6-by-8-inch liquid crystal
displays, all of which are physically identical and interchangeable.
These comprise two Primary Flight Displays, two navigation displays,
one engine parameter display, one system display and two Multi-Function
Displays. These MFDs are new with the A380, and provide an easy-to-use
interface to the flight management system—replacing three multifunction
control and display units. They include QWERTY keyboards and
trackballs, interfacing with a graphical "point-and-click" display
navigation system.
Engines
Either the Rolls-Royce Trent 900 or Engine Alliance GP7200 turbofan
engines may power the A380. Both are derived from those installed in
the 777. The Trent 900 is the scaled version of the Trent 800 but
incorporating sweptback fan and counter-rotating spools of the
stillborn Trent 8107. The GP7200 has GE90 derived core and PW4090
derived fan and low-pressure turbo-machinery. The Rolls-Royce Trent,
the launch engine, initially gained most sales. However, the Engine
Alliance GP7201 sales have grown, and now roughly match those of the
Trent 900.
Technological features
When the 747 replaced the Douglas DC-8 as the biggest airliner, the
technology used was essentially similar (similar flight controls,
hydraulics, electrics and avionics) but scaled up for the size. The
same however cannot be said about the A380 and the 747-400. As compared
to the Boeing 747 the colossal size of the A380 requires novel
approaches to application of technologies, especially for weight saving
purposes, in order for it to meet its performance guarantees. Many of
the technologies first used here may later be used by other jetliners
as operational experience is accumulated.
Materials
The new material GLARE is used in the upper fuselage and on the
stabilizers' leading edges. This aluminium-glass-fibre laminate is
lighter and has better corrosion and impact resistance than
conventional aluminium alloys used in aviation. Unlike earlier
composite materials, it can be repaired using conventional aluminium
repair techniques.
Carbon-fibre reinforced plastics, glass-fibre reinforced plastic and
quartz-fibre reinforced plastic are also used extensively in wings,
fuselage sections and on doors. The A380 marks the first time that
carbon fibre is used to make the central wing box of a commercial
airliner. Thermoplastics are used in the slats’ leading edges.
Newer weldable aluminium alloys are also used. This enables the
widespread use of laser welding manufacturing techniques—eliminating
rows of rivets and resulting in a lighter, stronger structure. While
Airbus intended to use GLARE across its future product line, Boeing's
decision to go all-composite with its 787 has forced Airbus to choose a
similar path with new materials on its A350.
Advanced avionics architecture
Integrated Modular Avionics (IMA)
IMA, first used in advanced military aircraft such as F/A-22 Raptor and
Eurofighter Typhoon, is the main avionics architecture. It is based on
commercial-off-the-shelf (COTS) design. Many previous dedicated
single-purpose avionics computers are replaced by dedicated software
housed in onboard processor modules and servers. This cuts the number
of parts as well as providing increased flexibility without resorting
to customised avionics. This reduces costs and benefits from the
cheaply commercially available computing power.
Avionics Full Duplex Switched Ethernet (AFDX)/ ARINC 664
The avionics data communication networks employed is switched-Ethernet
based AFDX following the ARINC 664 specifications. Together with IMA,
the A380 avionics is very highly networked. The data networks are
switched full-duplexed star-topology and based on 100baseTX
fast-Ethernet. This reduces wires required as well as eliminating
latency. The standard is based on widely approved and adopted standards
like Ethernet (IEEE 802.3) and IP/UDP (Internet Protocols). This
architecture is significantly more advanced than the bus-topology based
ARINC 629 used in Boeing 777.
Network Systems Server (NSS)
The NSS is the heart of A380 paperless cockpit. It eliminates the bulky
manuals and charts traditionally carried by the pilots. The NSS has
enough inbuilt robustness to do away with onboard backup paper
documents. The A380's network and server system stores data and offers
electronic documentation, providing a required equipment list,
navigation charts, performance calculations, and an aircraft logbook.
All will be accessible to the pilot from two additional 11-inch
diagonal LCDs. Each is controlled by its own keyboard and control
cursor device mounted in the foldable table in front of each pilot.
Power-by-wire flight controls
Power-by-wire flight controls actuators are used for the first time in
civil service. They function as ultimate flight control backups for the
A380. In certain conditions they help the primary flight controls
during certain manoeuvres. They have self-contained hydraulic and
electrical power supplies. They are used as electro-hydrostatic
actuators (EHA); used in some spoilers and as electrical backup
hydrostatic actuators (EBHA) for the rudder.
350 bar hydraulic system
This is an improvement over the typical 207 bar (about 3,000 PSI)
system found in other commercial aircraft since the DC4 Skymaster in
1942. First used in military aircraft like V-22 Osprey and F/A-18
Hornet, the use of a higher pressure reduces the size of pipelines,
actuators and other components for overall weight reduction. The 350
bar (about 5,080 PSI) pressure is generated by 8 de-clutchable
hydraulic pumps. Pipelines are typically made from titanium and the
system features both fuel and air-cooled heat exchangers. The
hydraulics system architecture also differs significantly from other
airliners. Self-contained electrically-powered hydraulic power packs,
instead of secondary hydraulic system, are the backups for the primary
systems. This saves weight and reduces maintenance.
Electrical generation
The A380 uses four 150kVA variable-frequency generators eliminating the
constant speed drives for better reliability. The A380 uses aluminium
power cables instead of copper for greater weight savings due to the
number of cables used for aircraft of this size and complexity. The
electrical power system is fully computerized and many contactors and
breakers have been replaced by solid-state devices for better
performance and increased reliability.
LED and High Intensity Discharge (HID) lighting
The A380 features a bulbless illumination system. LEDs are employed in
the cabin, cockpit, cargo and other fuselage areas. The cabin lighting
features programmable multi-spectral LEDs capable of simulating the
cabin ambience illumination from daylight to night and various shades
in between. HID lighting is used externally giving brighter, whiter and
better quality lights. The two technologies used are far superior to
the incandescent light bulb in terms of brightness and service life.
Electrical thrust reversers
Thrust reversers are one of the items that are often faulty in service.
The A380 was initially planned to do away with thrust reversers as it
has more than enough braking capacity. The FAA disagreed and Airbus
elected to fit the 2 inboard engines with them. The A380 features
electrical actuated thrust reversers. This gives better reliability
than their pneumatic or hydraulic equivalents beside saving
considerable weight.
Amenities
Initial publicity stressed the A380's space and comfort, allowing for
relaxation areas, bars, duty free shops and the like. The only A380
customer likely to use this configuration is Virgin Atlantic, which has
a bar in Business Class on most of its newer airliners and announced
plans to include casinos on their A380s. Similar items were proposed in
the past when large aircraft were announced, but airlines have always
opted for more seats to lower ticket costs. Given the history of the
airline industry, the A380 will significantly expand the improvements
that the 747 made—more seats and lower seat-distance costs - while
providing wider seats and better amenities. With 555 passengers, the
A380 represents a 35% increase over the 747-400 in standard three-class
configuration, along with a nearly 50% larger cabin volume - meaning
much more space per passenger. Some airports have planned terminal
reconfigurations to facilitate loading and unloading from the A380's
double-decker design.
Construction
Airbus operates 16 manufacturing sites across Europe, most of which
produce parts for the new A380 airliner.
First, the front and rear sections of the fuselage are loaded on an
Airbus RORO ship, Ville de Bordeaux, in Hamburg, northern Germany,
whence they are shipped to the United Kingdom. There the huge wings,
which are manufactured at Filton in Bristol and Broughton in north
Wales, are transported by barge to Mostyn docks, where the ship adds
them to its cargo. In Saint-Nazaire, western France, the ship trades
the fuselage sections from Hamburg for larger, assembled sections, some
of which include the nose. The ship unloads in Bordeaux. Afterwards,
the ship picks up the belly and tail sections in Cadiz, southern Spain,
and delivers them to Bordeaux.
From there, the A380 parts are transported by barge to Langon, and by
road to an assembly hall in Toulouse. New wider roads, extra canal
systems and barges were developed to deliver the massive A380 parts.
After assembly, the aircraft are flown to Hamburg to be furnished and
painted. Final assembly began in 2004, with first aircraft (MSN001)
displayed in January 2005.
|