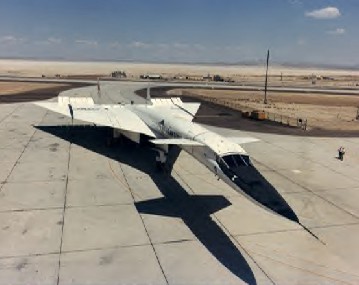
North American started with evident determination to overcome the drag of
supersonic flight. They worked on a canard design, with outer wing and fuel pod
units which could be detached, allowing the bomber to land at a little over a
quarter of its takeoff weight. In this first design the bomber was basically
built in three parts, a central pod that contained the engines, crew, some fuel
and the bombs, and two very large side units on the left and right that were
most of the wing and tail area, as well as containing large fuel tanks. The
result looked something like a very large P-38 Lightning, with the
central pod being much longer and including canards.
Normally the plane would "stay together" in one very large piece. It was over a
million pounds on launch, larger than a 747-400. On a combat mission the plane
would fly in this combination to enemy airspace at subsonic speeds. By the time
it arrived the fuel tanks in the outer portions of the wings would be empty, and
at that point the plane would "break". The outer wings and tail would fall off,
leaving the inner pod and the stubs of the wings. With very little of the plane
left, it would now have a huge power-to-weight ratio, so it would accelerate to
Mach 3 for a "dash" to it's target.
Curtis LeMay was not enthusiastic about the design, and is credited with the
response, "Hell, this isn't an airplane, it's a three-ship formation." North
American, as one contender for the WS-110 contract, had meanwhile been doing
their homework. They calculated that the amount of fuel needed to cruise at Mach
3 all the way to target turned out to be less than that needed to fly the same
distance at high subsonic speed. It would need more fuel flow, but the aircraft
would cover the ground faster.
Three times the speed would not require three times the fuel flow, but a good
deal less. This is a result of something called "wave drag", which means,
simply, that it's actually hardest to fly right under the speed of sound. As a
result, if they could produce a plane that could handle the heat, and has enough
thrust to get through that wave drag, they could fly faster without impossible
fuel demands. They proposed steel a construction because it could take the heat
of high speed flight, and it was cheap, a real concern if they were going to
build hundreds of them.
Their
design was eventually accepted, with the long, graceful fuselage lines, high
canard and delta wing, with tilting wing tips which served to trap compression
under the wing, providing additional lift. In wind tunnel tests it looked as if,
with newly developed high-performance aircraft fuels, compression lift would
assist the WS-110A aircraft to a cruise of Mach 3, a sustained speed which not
long before had been out of reach.
Use of ethyl borane fuel stood to further enhance the bomber's performance, and
RAF Flying Review of September 1958 dubbed WS-110 the "Boron Bomber". They
guesstimated from "unofficial reports" that it would fly at 100,000 feet, cruise
at Mach 2 with room for Mach 3 "dash" performance, and achieve a 6,000 mile
range without refuelling.
In 1958 the project came together, and the aircraft had a name, the B-70. After
passing through five separate company design numbers with North American, the
B-70 would go ahead as their design NA-278. It would be plagued by a series of
structural problems largely related to its ground-breaking technology, and very
soon changing government views would threaten the future of the project.
About 70% of the Valkyrie was to be of a new stainless steel. The
interior structure was mostly corrugated sheets, and the skin was a brazed
honeycomb sandwich of very thin steel, yet very strong. The parts most subjected
to heat were of a material never before used in an aircraft, René 41. Aerofoil
surface edges were machined to extreme sharpness.
The six GE engines were housed in an engine box under the wings, profiled to
generate compression lift. On "zip fuel" one engine alone made more noise than
any air-breathing engine in history. Development of the two prototypes was to
cost around $1,500M, making them the most expensive two aircraft built to that
date, and worth, according to one estimate, about ten times their weight in
gold.
In mid-1959, the B-70's future came into question, with enormous expenditure
going into missile systems. Manned aircraft were considered in some quarters to
be near-obsolete. To make matters more awkward, the expensive boron fuel program
was cancelled.
Then, in December 1959, the B-70 project itself was cancelled, except for
completion of a single prototype. The planned first flight was rescheduled from
January to December, 1962. It was still hoped that by 1966 an SAC wing might use
B-70s if the pro-missile lobby could be persuaded to change their views.
After a review in 1960, the program was partially restored, and allowance was
made for up to twelve fully-operational B-70s to be built, in addition to the
prototype. In March 1961, during the Kennedy administration, it was still held
that missile development made the B-70 unjustifiable. It was reduced to the
status of a Mach 3 research project, with an airframe potentially useful as a
bomber. Secretary of Defence Robert McNamara promptly cut back the program to
three prototypes, which were ordered on 4th October, 1961; but the third was
cancelled a few weeks later, leaving only aircraft with the USAF numbers 62-001
and 62-207.
The USAF tried to keep some promise in the project by changing the role of the
B-70 to strike-reconnaissance late in 1962, and temporarily redesignated the
aircraft RS-70. They proposed an initial delivery of sixty RS-70s to enter
service in 1969 and a further 150 the year after. Apart from a slight flicker of
interest from the House Armed Services Commission, it was wishful thinking on
the USAF's part, the more so when the existence of the purpose-built Lockheed
A-12, which had also been under development since the late 1950s, was revealed
to President Johnson late in 1963 and announced to the world in February 1964.
The first XB-70 was nearly complete in late 1962 when electrolytic corrosion
between the various grades of steel used in its structure was discovered.
Extensive inspection and rebuilding took up a further two years. In 1963 funding
dried up, and the XB-70 project was left to starve, existing only as a research
project. The first flight was pushed ahead to late 1963 for the first prototype,
and mid-1964 for the second.
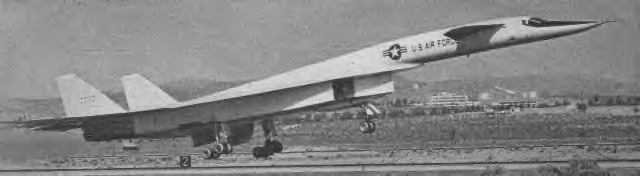
Assembly
of the first XB-70A was completed in mid-1963, but solution of a fuel leak
problem took another eighteen months. Finally, on May 11, 1964, the XB-70A
emerged from its hangar at Palmdale, California. Earlier releases of information
had not fully prepared its audience for its size, its sleek lines, and its
poised menace.
The canard design enabled the foreplane to be used to assist with trimming the
aircraft across a wide speed range from a minimum 150 kts. (278 km/h) landing
speed, up to Mach 3; they could also serve as flaps. The compression lift
derived from the shock wave at the front of the intakes was a retained benefit,
and apart from boosting lift by as much as 30%, also reduced drag by allowing
shallower angles of attack. The tilting wing tips were kept level on takeoff,
and tilted down to 25° at low speeds and altitudes. They served to minimise trim
changes in pitch. At high speeds and altitudes, they would be dropped further,
to 65°, enhancing compression lift.
A variable-geometry system was fitted to the nose, allowing a ramp forward of
the cockpit to be raised for supersonic flight or lowered for a direct forward
view. This visor was merely aerodynamic. The cockpit was sealed behind a
vertical pressure-bearing flat screen.
Inside their compartment, the four crew members were provided with airliner
comfort and could work in their shirt-sleeves. They sat in cocoon-like seats
with clamshell doors which, in the case of pressurisation loss, would provide
them with individual sealed escape capsules. The capsules contained their own
oxygen bottles and emergency supplies, and basic controls to close the throttles
and trim for an emergency descent, whilst monitoring the instruments through a
window in the capsule. The capsules could be re-opened at a safe altitude, or
rocket-ejected through jettisonable roof panels.
A single bay between the engine ducts and engines could carry groups of any
nuclear bombs used by SAC. The bay had doors which slid open automatically at
the last moment before weapon release. Although not part of the requirement,
studies were also made into various external ballistic weapon loads.
On
its first flight on 21st September, 1964, the XB-70 was flown by Colonel Joe
Cotton and North American's chief test pilot Alvin S. ('Al') White. The aircraft
failed to achieve Mach 1 due to an inability to retract the main undercarriage.
Number 2 engine suffered foreign object damage; and another fault locked the two
left rear main tyres, which blew on touchdown. In general, flight development
was encouraging and proceeded much as predicted.
Both prototypes reached Mach 3 for the first time on their 17th flights,
respectively on October 15th, 1965 and January 3, 1966. The XB-70A was flown for
the first time using the crew capsule controls on December 20, 1965.
On 8th June, 1966, aircraft 62-207 was to complete various tasks then pose, with
a small group of other General Electric-engined aircraft, for some publicity
shots for GE. Al White was to be pilot. As the work load was light, Maj. Carl S.
Cross was allowed on board for his first ride as co-pilot. Accompanying the
XB-70 were a McDonnell F-4 Phantom of the US Navy; a Northrop F-5 and a
Northrop T-38 (both North American crewed); and an F-104 Starfighter
flown by NASA pilot Joe Walker, who had flown the X-15.
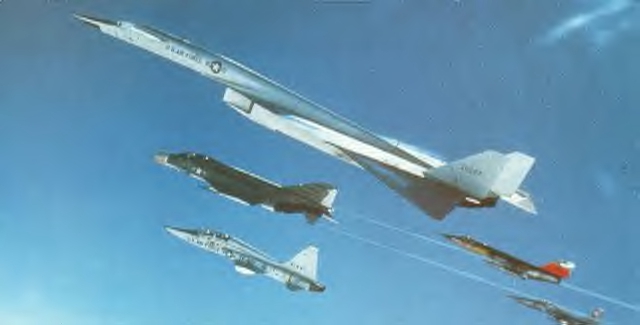
The
formation was controlled by a GE-engined Learjet, with no radio frequencies in
common with the XB-70. Radio messages had to be relayed via Edwards AFB. GE got
a number of good photos by 9.30 am. and ended the photo session about 9.35.
Apparently against the dictates of common sense, the NASA F-104 was edging up
close to the XB-70, finally moving in below the right wingtip.
The 30° crank-down of the Valkyrie's wingtips generated a strong vortex,
and this whipped the F-104 upside-down and across the top of the larger
aircraft's wings. It took away almost all of the XB-70's tail fins. The F-104
fell back in a ball of fire; the Learjet resumed picture-taking.
For
some seconds the Valkyrie flew steadily, then began a slow roll, turning
into a violent yawing. Descending flat-on to the airflow, a large part of the
left wing broke away. Soon after, White ejected in his crew capsule. The XB-70
stopped oscillating and fell, slowly rotating, hitting the ground almost flat
about four miles north of Barstow. Why Maj. Cross, with 8,528 flying hours,
failed to eject is unknown, and he died in the crash.
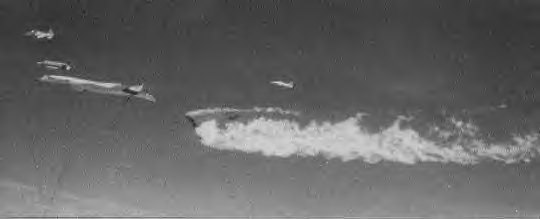
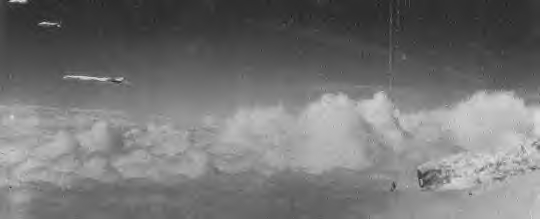
Perhaps unfairly, GE suffered a great deal of ill-will for the incident,
although they had done nothing wrong, and for some time it was impossible to
arrange PR exercises and aerial photography.
The surviving XB-70, 62-001, continued to amass research data, largely for NASA.
Its last flight was on 4th February, 1969, to the USAF Museum, Wright-Patterson,
where it remains, alongside the Convair B-36, the largest aircraft on display.
SPECIFICATIONS
Span: 105 ft.
Length: 185 ft. 10 in. without boom; 192 ft. 2 in. with boom
Height: 30 ft. 9 in.
Weight: 534,700 lbs. loaded
Armament: None
Engines: Six General Electric YJ-93s of 30,000 lbs. thrust each
with afterburner.
PERFORMANCE
Maximum speed: 2,056 mph. (Mach 3.1) at 73,000 ft.
Cruising speed: 2,000 mph. (Mach 3.0) at 72,000 ft.
Range: 4,288 miles
Service Ceiling: 77,350 ft.