
planform design and other
issues
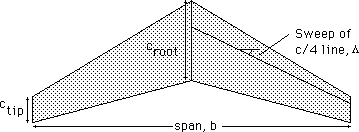
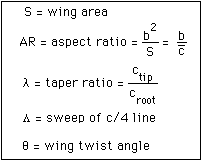
Span
Selecting the wing span is one of the most basic
decisions to made in the design of a wing. The span is sometimes constrained by
contest rules, hangar size, or ground facilities but when it is not we might
decide to use the largest span consistent with structural dynamic constraints
(flutter). This would reduce the induced drag directly.
However, as the span is increased, the wing structural weight also increases and
at some point the weight increase offsets the induced drag savings. This point
is rarely reached, though, for several reasons.
The optimum is quite flat and one must
stretch the span a great deal to reach the actual optimum.
Concerns about wing bending as it affects
stability and flutter mount as span is increased.
The cost of the wing itself increases as the
structural weight increases. This must be included so that we do not spend 10%
more on the wing in order to save .001% in fuel consumption.
The volume of the wing in which fuel can be
stored is reduced.
It is more difficult to locate the main
landing gear at the root of the wing.
The Reynolds number of wing sections is
reduced, increasing parasite drag and reducing maximum lift capability.
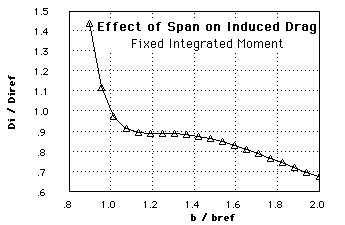
On the other hand, span
sometimes has a much greater benefit than one might predict based on an analysis
of cruise drag. When an aircraft is constrained by a second segment climb
requirement, extra span may help a great deal as the induced drag can be 70-80%
of the total drag.
The selection of optimum wing span thus requires an analysis of much more than
just cruise drag and structural weight. Once a reasonable choice has been made
on the basis of all of these considerations, however, the sensitivities to
changes in span can be assessed.
Area
The wing area, like the span, is chosen based on
a wide variety of considerations including:
Cruise drag
Stalling speed / field length requirements
Wing structural weight
Fuel volume
These considerations often lead to a wing with the smallest area allowed by the
constraints. But this is not always true; sometimes the wing area must be
increased to obtain a reasonable CL at the selected cruise
conditions.
Selecting cruise conditions is also an integral part of the wing design process.
It should not be dictated a priori because the wing design parameters will be
strongly affected by the selection, and an appropriate selection cannot be made
without knowing some of these parameters. But the wing designer does not have
complete freedom to choose these, either. Cruise altitude affects the fuselage
structural design and the engine performance as well as the aircraft
aerodynamics. The best CL for the wing is not the best for the
aircraft as a whole. An example of this is seen by considering a fixed CL,
fixed Mach design. If we fly higher, the wing area must be increased by the wing
drag is nearly constant. The fuselage drag decreases, though; so we can minimize
drag by flying very high with very large wings. This is not feasible because of
considerations such as engine performance.
Sweep
Wing sweep is chosen almost exclusively for its
desirable effect on transonic wave drag. (Sometimes for other reasons such as a
c.g. problem or to move winglets back for greater directional stability.)
It permits higher cruise Mach number, or greater
thickness or CL at a given Mach number without drag divergence.
It increases the additional
loading at the tip and causes spanwise boundary layer flow, exacerbating the
problem of tip stall and either reducing CLmax or
increasing the required taper ratio for good stall.
-
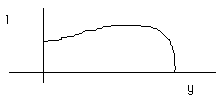
It increases the structural
weight - both because of the increased tip loading, and because of the increased
structural span.
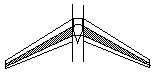
It stabilizes the wing
aeroelastically but is destabilizing to the airplane.
Too much sweep makes it difficult to accommodate
the main gear in the wing.
Thickness
The distribution of thickness from wing root to
tip is selected as follows:
- We would like to make the t/c as large as
possible to reduce wing weight (thereby permitting larger span, for example).
- Greater t/c tends to increase CLmax
up to a point, depending on the high lift system, but gains above about 12%
are small if there at all.
- Greater t/c increases fuel volume and wing
stiffness.
- Increasing t/c increases drag slightly by
increasing the velocities and the adversity of the pressure gradients.
- The main trouble with thick airfoils at high
speeds is the transonic drag rise which limits the speed and CL at
which the airplane may fly efficiently.
Taper
The wing taper ratio (or in general, the
planform shape) is determined from the following considerations:
- The planform shape should not give rise to an
additional lift distribution that is so far from elliptical that the required
twist for low cruise drag results in large off-design penalties.
- The chord distribution should be such that
with the cruise lift distribution, the distribution of lift coefficient is
compatible with the section performance. Avoid high Cl's which may
lead to buffet or drag rise or separation.
- The chord distribution should produce an
additional load distribution which is compatible with the high lift system and
desired stalling characteristics.
- Lower taper ratios lead to lower wing weight.
- Lower taper ratios result in increased fuel
volume.
- The tip chord should not be too small as
Reynolds number effects cause reduced Cl capability.
- Larger root chords more easily accommodate
landing gear.
Here, again, a diverse set of considerations are important.
The major design goal is to keep the taper ratio as small as possible (to keep
the wing weight down) without excessive Cl variation or unacceptable
stalling characteristics.
Since the lift distribution is nearly elliptical, the chord distribution should
be nearly elliptical for uniform Cl's. Reduced lift or t/c outboard
would permit lower taper ratios.
Evaluating the stalling characteristics is not so easy. In the low speed
configuration we must know something about the high lift system: the flap type,
span, and deflections. The flaps- retracted stalling characteristics are also
important, however (DC-10).
Twist (washout)
The wing twist distribution is perhaps the least
controversial design parameter to be selected. The twist must be chosen so that
the cruise drag is not excessive. Extra washout helps the stalling
characteristics and improves the induced drag at higher CL's for
wings with additional load distributions too highly weighted at the tips.
Twist also changes the structural weight by modifying the moment distribution
over the wing.
Twist on swept-back wings also produces a positive pitching moment which has a
small effect on trimmed drag. The selection of wing twist is therefore
accomplished by examining the trades between cruise drag, drag in second segment
climb, and the wing structural weight. The selected washout is then just a bit
higher to improve stall.
|