
Flying the Cessna C172
by
Gene Whitt
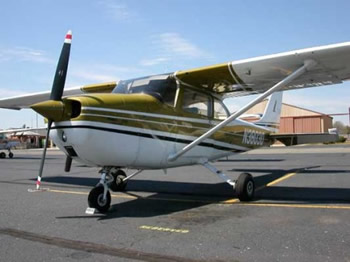
C-172 Information
C-172 Model (Re-engined model N)
1955 to 1986 C-172 Differences
Lycoming
Takeoff/Landing Comparison
C-172 Differences and Checkout
Damaging Aircraft
Exercise in C-172
C-172 Procedures; and Landings
Precision Approach Speed No
Flaps
Level Cruise
Climb at 90 Knots
Level Approach Speed at 90 Knots
Level Approach Speed at 90 Knots
#2
Approach Descent Speed at 90 Knots
Slips with Flaps
Landing Problem
Second Opinion
Fuel Problems of Cessnas
C-172R Data Sheet
A Better Way to Move a Cessna
Cessna vs Piper
Aircraft Proficiency Checkout
Modified C-172s
1963 C-172
Suggestions
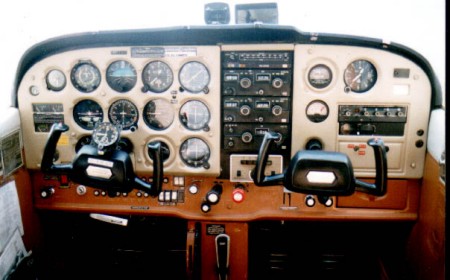
C-172 Information
This TCDS covers all 172s. For models 172 through early 172Ms the Vfe
limitation is 87 knots. From later 172Ms through the 172R the Vfe limitation is
85 knots. This is the highest speed, in general, that the pilot should extend
*full* flaps.
C-172 FAA Type Certificate Data
In the case of the 172 SP, the W&B limitations are contained in FAA Type
Certificate Data Sheet (TCDS) 3A12 (which covers all 172s) Note 1 which states:
XII - Model 172S, Skyhawk SP, 4 PCLM (Normal Category), 2 PCLM (Utility
Category), Approved May 1, 1998
C.G. Range Normal Category
(1) Aft Limits 47.3 inches aft of datum at 2,550 pounds or less.
(2) Forward Limits Linear variation from 41.0 inches aft of datum at 2,550
pounds to 35.0 inches aft of datum at 1,950 pounds; 35.0 inches aft of datum at
1,950 pounds or less.
Utility Category
(1) Aft Limits 40.5 inches aft of datum at 2,200 pounds or less.
(2) Forward Limits Linear variation from 37.5 inches aft of datum at 2,200
pounds to 35.0 inches aft of datum at 1,950 pounds; 35.0 inches aft of datum at
1,950 pounds or less.
The key to the 400-pound limitation you see on your chart is derived from the
shifting datum line at the variable weights. The manufacturer determined that
there should (actually must) be a 400-pound limitation for the two front seats
in order to meet the structural limitations contained in the regulations.
C-172 has best G.A. fatal accident record at .56 per 100,000 flight hours. This
figures out to one accident for every 18,000 hours of C-172 flight. Using the
figure that the average serious injury/fatal accident occurs in only one of
every six accidents, we find that an injury accident will occur 110, 000 hours
of flight time. I want to fly long enough to have an injury accident.
Not long ago I saw four people get into the C-172. I questioned the pilot
regarding weight and he said that he was in limits. When the heavyweight of the
group got into the back seat, I again approached the pilot and suggested that
balance might be a problem. What can be done? First, I don't believe anyone
deliberately, and knowingly damages an aircraft or exposes passengers to danger.
A pilot may have erroneous perceptions as to what makes a good landing. Maybe,
there is a problem with knowing aircraft attitudes. Is establishing a stabilized
approach at a constant airspeed the problem? Very possibly, it is caused by a
situation beyond the pilot's experience. Instructional flying is five times
safer than other G.A. flying. Since so much instruction is done in the C-172 it
is logical to expect that the C-172 has an excellent safety record when compared
to complex-high-performance aircraft.
A single pilot in a C-172 with his seat well forward; the C-172 with a a full
radio stack; and The aircraft is within C.G. limits presents a potential flying
control problem. A final approach at 60 knots will give the elevators enough
authority to round out. As the aircraft decelerates below 60 knots the elevator
loses authority and may well be unable to raise the nose, even if full back and
up. This is especially true if the power has been taken off.
Under these conditions, what should the pilot do? If you can't arrange to get
one passenger in the back seat, you should plan to leave at least 1200 rpm. The
power will help hold the nose up and give the elevator the authority required
for a full stall landing. Very careful energy management will be required to
avoid a balloon. It can be done to a full stall landing every time. You will not
be able to see the runway. The nose wheel will remain well clear of the ground.
Power can be applied for the takeoff and the flaps removed without the nose
wheel ever touching the ground. Alternatively, the power can be taken off as the
nose wheel touches.
Aircraft damage due to landings is mostly accumulative. Occasionally damage
happens all at once but usually it is accumulative. The gearbox can take
thousands of average landings without any damage. The spring gear can take a
heck of a beating. The severe damage to Cessnas is to the gearbox underneath the
seats. One falling out of the sky from 20' can break the box. Repair or
replacement of a C-172 gearbox can cost $9,000. The nose gear is attached to the
firewall. A very hard landing on the nose wheel can damage the firewall.
Flying an aircraft with a bent firewall is enough to trigger an FAA
investigation. Try to inspect the firewall of a C-172 or C-182 without removing
the cowling. Is the nose wheel fork bent? Inadequate preflight the FAA calls it.
It took me 14 months to shake them loose.
The C-172 generic landing uses 70 knots for downwind and final adding two
ten-degree notches of flaps while taking off two full turns of trim. On final
you put in full flaps and no trim change. You are on a stabilized approach
hands-off at 60 knots. For the go-around, on bringing up the flaps you will be
trimmed for a 75-knot climb. The hard part of flying the C-172 is levelling off.
The old joke about how long it take a student to level off a C-172 is answered
with, "Thirty-five hours". It will take about one and one-third turns of trim
and a close eye on the altitude while the plane accelerates. The trick is to
reduce to 2450 as soon as you reach 100 knots. Otherwise, you will be jockeying
airspeed and trim for quite a while. The cause of this problem is that the C-172
has less power for its weight than the C-150. The time to accelerate to 100
knots seems to take forever. Initially you will be holding backpressure and then
forward pressure on the yoke while the airspeed gets sorted out. Due to
deceleration the C-172 power should only be reduced to 1700. At approach speed
the power will have dropped to 1500 rpm
Top of page

C-172 Model M (Re-engined to model N)
The change of 1407U to a C-172N by the addition of the 160 H.P. engine will
increase the fuel consumption rate to around 8+ gph. I would suggest each pilot
run some fuel consumption tests to compute figures for their mode of operation.
To do otherwise is unsafe.
Note: Use of a C-172 information manual other than for a C-172N will give
erroneous information.
Power: New engine 1995 is 160 h.p. and has higher fuel consumption than previous
150 h.p. Fly conservative until consumption is known. Speed: Do not use manual
figures. For cross-country the use of 105K will work about right.
C-172 Information 1407U C-172 Model N. The new engine makes it Model N since the
flap deflection has been limited to 30 degrees.
Speed: Do not use manual figures for cross-country. The use of 105 kph will work
about right. This may change with new 160 hp engine but not by much. Power
mostly affects rate of climb. Cruise: Recommended lean mixture with fuel
allowance for engine start, taxi, takeoff, climb and 45 minutes reserve at 45%
power. 75% power at 8000' Range 450 nm no reserve. Cessna has a bulletin on the
C-152 that indicates full rich operations will decrease range by over an hour
and increase fuel consumption by 40%. Similar figures would probably apply to
the C-172.
C-172M 1975-6
hp - 150
Gross - 2300
Empty - 1335
Useful - 965
Cruise - 122kts
Climb - 643
New - 27,600
Current 41,500
Value retention 141%
Time 3.9 (Recommend 3 hours maximum)
Sea Level rate of climb 770 fpm
Service Ceiling 14,200
Takeoff Performance
Ground roll 865'
Over 50' obstacle 1440
Landing Performance
Ground roll 520'
Over 50' obstacle 250
CAS Stall Speed
Clean power off 50 kts
Dirty power off 44 kts
Empty weight and useful load.......consult weight and balance papers
C-172 is vulnerable to dangerous weight and balance conditions.
Gross to/landing weight 2300 lb.
Baggage allowance 120 lb.
Wing Loading 14.4
Fuel Capacity 42 gallons
Useable 39 gallons
Fuel consumption...................160 h.p. engine in 1995 changes figures
Engine- Lycoming 160 hp. (14.4 lb. per hp)
At 2500 rpm at 2000' 76% power and leaned uses 8.5 gph.
At 2400 rpm at 8000' 60% power 6.7 gph
The N has 160 hp and 30 degrees of flaps. These make it possible to increase the
useful and gross because of the go-around requirements. Slips with flaps are
either prohibited or not recommended in the POHs. The slip problem arises from
the possibility of extended flaps under certain conditions such as in slips or
wind shear blocking or interfering with the airflow over the horizontal tail
surfaces. I have had such an occurrence in a C-150. The tail surfaces stall and
the nose pitches straight down before the stall warner has a chance to yelp.
Cessna merely admits that there may be control oscillations.
Top of page

1955 to 1986 C-172 Differences
36,000 C-172s have been manufactured since the first one in June of 1955.
The C-172 has the best safety record of aircraft in its class. The 1956 model
had a 145 hp Continental. The 1960 model had a swept tail. In 1963 a rear window
appeared as well as single piece windshield and longer elevator. The 1956 to 60
C-172 had a low panel that allowed the pilot to 'look down' over the 145 H.P.
engine. Over 30,000 C-172s have been built in 43 years. 1960-63 enter the swept
tail and no-window fuselage. Enter the window in the back and then we have a
series of changes in engine, landing gear, and cockpit but essential things
remained the same. The 1964 model had electric flaps instead of the Johnson Bar.
1968 models switched to Lycoming 150 hp engines. In 1971 the spring steel gear
was changed to tubular. In 1972 the dorsal fin was extended to correct pitch
problems during slips. 1973 changed the wing leading edge to a droop as well as
a shorter propeller. An engine change in 1972 was a disaster due to inadequate
lubrication. 1978 saw the 24-volt electrical system and better seats. 1981 gave
a 160-hp engine and gross weight of 2400lbs but reduced flap travel of 30
degrees. 1986 changed the angle of the horizontal stabilizer to improve pitch
authority. Popular modifications include such things as 180 hp engines and
possibly constant speed props. Sound reduction through use of thicker
windshield, long range tanks and electronic upgrades are common.
The large slotted flaps in older Cessnas can a nose down pitch in forward slips.
A cautionary warning is in many POHs indicating that slips should be avoided
when using maximum flaps. The pitching motion is the result of the difference
between a strong wing downwash over the tail in straight flight to a reduced
downwash influenced by a raised aileron in slipping flight. This effect is
elusive hard to duplicate, I have experienced it only once in over 9000 hours.
This restriction does not apply to the wing-low drift correction used in
crosswind landings.
When the larger dorsal fin was adopted in the 1972 C-172L, this sideslip pitch
event was eliminated. In the higher-powered C-172s the placard was applicable to
a mild pitch from flap outboard-end vortex hitting on the horizontal tail at
some combinations of side-slip angle, power and airspeed."
Over sixteen C-172s are involved in accidents every month. One accident every
two days. This gives a rate per 100,000 flight hours of 1.46. Prior to 1977 the
C-172 engine failure rate was one per every 5.6 million hours of operation. Only
one in six of these accidents result in personal injury. Night accidents in
C-172 occur at nearly a 20% higher rate than day accidents.
85% of all C-172 accidents are due to pilot error. This is more than accidents
in other types. The aircraft has been deemed responsible in 7% of the accidents.
The percentage of C-172 accidents is highest when the pilot involved has between
100 and 200 hours of flight time. 50% of the accidents occurred when the pilot
had less than 50 hours in the C-172 type aircraft. A high percentage of C-172
accidents have been attributed to inadequate checkouts.
C-172s have twice as many hard
landings as a PA-28 (Cherokee) per aircraft. The C-172 is four times as likely
to have a wind related accident. It has twice as many go-around accidents. NRI
Flying Club has spent no less than $4,500.00 in the last two years on just
nose-strut repair and nose gear rebuilding of O7U. This is certainly indicative
of a problem in piloting, checkouts, and instruction. Making flat landings or
nose wheel first are the problem.
The C-172 has half as many fuel exhaustion accidents as like powered low-wing
aircraft. Crosswind takeoff and landing accidents were relatively frequent and
attributable to inadequate checkouts. The second major area of accident was the
go-around, which has been partially corrected by Cessna by reducing flap
extension to only 30 degrees on later models. Serious C-172 accidents were
generally related to controlled flight into terrain or obstructions. (Low level
flight) To fly the C-172 you must practice landing in different flap
configurations and power settings. You must know how to hold the control for
taxiing. The C-172 go-around requires anticipation and attention to the
procedures for flap removal. It takes practice of the right kind to bring an
improvement and a change in our maintenance costs. Years ago the Club lost a
C-172 because the pilot attempted to make a go-around without removing at least
partial flaps.
Airworthiness Directives are less common to the C-172 than other aircraft. Check
the security of the aileron counterbalance weights, seat tracks for locking,
flaps for smoothness of jack screw, and the panel lighting rheostat and you have
the ADs pretty well covered.
Top of page

Lycoming
First decide that aircraft is idling correctly
1. Operate engine for 1- minute at 1200 rpm. This might be done taxiing but it
is relatively hard on the brakes.
2. Increase to 1800 for 20-seconds
3. Reduce to 1200 rpm and kill with mixture.
Top of page

Takeoff/Landing Comparison
C-150 Take Off 735' /50' 1385 Landing Distance 445 /50' 1075
C-172 Take Off 945 /50' 1685 Landing Distance 550 /50' 1295
--C-172 Use 10 degrees for soft field or short roll but not for obstacle
clearance.
C-182 Take Off 795 /50' 1625 Landing Distance 545 /50' 1285
An airplane should not be
expected to get out of a space where it has landed.
Top of page

C-172 Differences and Checkout
Be careful loading a C-172. A C-172 has four seats but is really a three
passenger aircraft. Avoid putting weight in the back. C.G. is critical. What you
can carry and where you can carry it will depend on the individual situation.
Fuel consumption can cause a shift in the C. G. range. Useful load varies
because of installed equipment that is included in the empty weight. Fuel
consumption will vary with the loading. A heavy C-172 will require fuel after
less than three hours of flight. Don't believe the manual on range, speed,
capacity, or fuel consumption.
The time of year (temperature) has a significant effect on C-172 performance.
Aircraft performance early in the morning or in the winter will decrease at
warmer temperatures. What the C-172 was able to do in the winter, it will not be
able to do in the summer. Warm air does not have the same ground effect as cool
air. The C-172 is NOT a good high altitude or density altitude aircraft. C-172
performance requires careful planning, loading, cruise, and flight procedures.
Some of the performance for the C-172 at gross is poorer than that of the Cessna
two-seaters. The C-172 takes longer to accelerate to its cruise of 100+ Kts than
a C-150 does to its cruise of 85 Kts. Your first takeoff in a C-172 will
surprise you as it departs for the left side of the runway when power is
applied. You must anticipate this P-factor and torque with right rudder.
Controls are heavier and response slower than trainers. Correct trim use becomes
important. Failure to anticipate trim settings is a typical pilot problem.
Trim adjustments must be made during the descent and fine adjustments made when
level. If the climb and level off is done at assigned altitude, then the plane
must be deliberately over trimmed to require backpressure to hold the altitude.
The altitude must be held for up to three minutes at higher density altitudes
before any power reduction. This allows the plane to accelerate rather than
climb.
The most important adjustment between flying the C-150 and the C-172 is in
performing the transition from climb to level cruise. For the next several
minutes the airplane will proceed to both accelerate and climb. The 'new to
type' pilot will be several hundred feet high and have to go through the
levelling process all over again. Because of its power to weight ratio and drag,
the C-172 takes a while to accelerate from climb to cruise speed.
The pilot must be prepared to anticipate the amount of trim setting and yoke
pressures required to maintain altitude for the time it takes the C-172 to
accelerate to 100 kts. At 100+ knots the power should be reduced to 2450 rpm and
trim adjusted. Even slight changes in altitude or power during this transition
can make the transition to level flight take much longer. If the climb and level
off is to be done at an assigned altitude, then the plane must be deliberately
over-trimmed to require backpressure to hold the altitude during acceleration.
The most common fault in levelling off is to trim for level flight immediately
and then proceeding to other activities. For the next several minutes the
airplane will proceed to both accelerate and climb. The 'new to type pilot' will
be several hundred feet high and have to go through the levelling process all
over again. One solution for this is to climb 1 to 2 hundred feet higher than
the desired altitude and then dive and accelerate to the assigned altitude. (Not
an IFR procedure) Trim adjustments must be made during the descent and fine
adjustments made when level.
The C-172 can be flown just like a C-150, however, to do so is both uneconomical
and a sign of incompetence. In several very important particulars the C-172
should be flown differently than the C-150. While the C-172 may have more
horsepower than the C-150, it actually has less power per pound. The C-150 can
be made to climb at gross with full flaps. The C-172 has difficulty just to
maintain altitude. Any go-around with a C-172 must include removing the drag due
to flaps. Because of its power to weight ratio, the C-172 takes a while to
accelerate in any situation. The new 160 h.p. engine will help but only
marginally. Additional power benefits climb more than any other performance
factor.
The C-172 has a much higher and deeper instrument panel, which may require
shorter pilots consider putting their flight materials into a pillow type
carrying case. When level, the C-172 seems to have a slightly nose down attitude
somewhat different than that of a C-150. In level flight the nose is low enough
to be easily seen over. The C-172 nose position is one of the transitions you
need to get used to. The C-172 now has a four position fuel selector. An
imbalance in fuel use can be corrected only by going to the fullest tank for a
period of time. Don't try to put the selector part way or your engine will stop.
Older C-172s require single tank operation above 5000'.
If the trainee has been taught to slow the C-150 on airport arrival prior to the
numbers, this rather uneconomical technique will carry over to the C-172. The
fact is that the extra speed of the C-172 on downwind will give the correct
pattern size and spacing if properly used. For instance, to obtain 1500 RPM in
the C-172 the throttle setting should initially be reduced only to 1700 RPM. As
the aircraft decelerates at the pattern altitude, the RPM will fall to 1500 RPM.
The entire transition process becomes very easy if the constants of trim, power
setting, airspeed, are carried from the C-150 to the C-172. The pattern speeds
of the C-172 may be different from downwind, and, base. These speeds while
different are constant. Slow to 80 knots after the numbers, 70 knots on base and
60 knots for final. Other speed sequences will work just as well.
The older C-172, like the C-150, has a built in engineering relationship between
power setting, flap application, and trim. Knowledge of these factors allow a
pilot to 'know' what power, flap and trim settings will give the 'hands-off'
performance desired. The C-172 requires full movement of the trim for no flap
slow flight and only 17/1800 RPM. Abeam the numbers, three down trims and power
to 1700 from cruise will give 70 kts and 1500 RPM at the key position just
before base. A one for one with 10 degrees of flaps and trim will maintain 70
kts until turning final. On final full flaps will not require any additional
trim and the approach speed will fall to 60 kts. After landing and flaps up, the
aircraft is properly trimmed for climb. (Likewise, the C-152)
The flap and no-flap pattern and approach speeds of a C-172 can be the same. The
use of flaps improves the aiming descent angle on final and can reduce the
ground impact speed. Proper flare in a C-172 greatly reduces structural loads
and touchdown speed. You must work to get a full-stall minimum speed touchdown
in the C-172. The C-172 tends to lose elevator power in flare and will be unable
to raise the nose unless the elevator effectiveness is augmented by prop-wash.
Try landing with 1200 rpm and see the difference attained in nose attitude. The
landings are even easier with less than 40-degrees of flap.
The landing configuration with flaps means that the runway will not be in view
for a proper (full stall) landing. The C-172 nose position is one of the
transitions you need to get used to both for level and landing. Good landings of
the C-172 with the nose wheel off the ground require precise use of yoke, flaps,
and power. To fly the C-172 you must practice landing in different flap
configurations and power settings. You must know how to hold the control for
taxiing. The C-172 go-around requires anticipation and attention to the
procedures for flap removal. Evidence based on NRI maintenance would indicate an
on-going problem.
One of the more difficult aspects of making the transition to a C-172 is
directly related to its power to weight ratio. The C-172 takes longer to achieve
cruise speed when levelled off than do most other aircraft. The traditional
saying is, "How long does it take a student to level off a C-172?" (Answer
below)
I have found it desirable to initiate the instruction from established cruise
airspeed with power at 2450 rpm. Note the airspeed indicated at cruise. Have the
student index (memorize) the amount of trim change required to establish a
hands-off climb at 75 knots at full power. With this information a student can
learn to level off a C-172 quite quickly as well as initiate a stabilized climb.
I have found many students who come to me with prior instruction tend to level
off with an initial reduction to cruise power. WRONG! This means that a C-172
must accelerate to cruise speed using cruise power. It will take several minutes
and a constant adjustment of the trim. Typical result is for the aircraft
winding up 200' high and still out of trim. Students using this method will take
35 hours to learn to level off.
The most efficient way to level off a C-172 is to leave climb power full on
during the initial levelling off. Use the yoke to lower the nose and forward
pressure to hold heading and altitude. Roll the trim wheel up one full turn and
perhaps a half more. Continue holding the heading and altitude while the
aircraft accelerates to cruise speed. Use sound as an indicator as to when you
should take a look away from the horizon and to the airspeed indicator. At
cruise speed reduce power to 2450.
Exceeding cruise speed or being below cruise speed before reducing the power
means that your trim setting as indexed will be wrong. This means you must hold
heading and altitude with yoke pressure until the aircraft acquires its natural
cruise speed. This problem is easily avoided by reducing the power at the proper
time. One way to check the level cruise attitude and trim is just to place both
hands on the cowling pad and note that the nose begins to drop. Put your hands
over your head and the nose rises. Normal hand position gives level flight.
The more accurately you determine normal cruise speed and the index of trim
difference between climb and level the faster you can level off. For those who
are working on their IFR rating you might work on additional trim/power indexes
as required for 90 knot climbs, level, and descents. Learn the sounds of your
aircraft just as you know the sounds of your automobile. With a safety pilot
practice making the throttle and trim changes with your eyes closed...it can be
done and makes it so that flying the airplane is not a part of the IFR problem.
For a given configuration (Weight, flaps, gear, etc.) Pitch + Power =
Performance. Otherwise, if you pitch to Vy attitude, add full power on your
Skyhawk you expect to get about 75kts airspeed and 700 fpm climb (Performance).
(Standard conditions +10-20 degrees.)
Useful information to know would be the pitch attitude and power setting (RPM)
to use to maintain altitude, descend at 500 fpm and climb at 500 fpm while
holding 75 kts airspeed. Do the same for 65 and 85 kts. For highest speed flying
go to 7500 feet with 2700 rpm and leaned. For fuel efficiency use 2500 rpm for a
10% fuel saving.
If you can fly the same aircraft most of the time you can develop a sense, which
will help you immensely. Set any configuration you want, and listen to the
sounds. By changing the configuration you can get an ear for the next set of
specific sounds. You can literally learn to tune your aircraft by ear. You can
find a functional relationship between RPM and air speed in a specific
configuration.
Top of page

Damaging Aircraft
Aircraft damage due to landings is mostly accumulative. Occasionally it
happens all at once but usually it is accumulative. The gearbox can take
thousands of average landings without any damage. The spring gear can take a
heck of a beating. The severe damage to Cessnas is to the gear box underneath
the seats. One falling out of the sky from 20' can break the box. Repair or
replacement of a C-172 gear box can cost $9,000. The nose gear is attached to
the firewall. A very hard landing on the nose wheel can damage the firewall.
Flying an aircraft with a bent firewall is enough to trigger an FAA
investigation. Try to inspect the firewall of a C-172 or C-182 without removing
the cowling. Is the nose wheel fork bent? Inadequate preflight the FAA calls it.
It took me 14 months to shake them loose.
The accumulative damage mostly occurs to the nose gear. The oleo strut can
survive forever if the landings are on the main gear. When the nose wheel
becomes a part of the initial landing contact it becomes life limited. Every
compression of the strut loses some air and perhaps oil. If the strut is not
cleaned prior to every flight the accumulated oil and dirt act like sandpaper on
the 'O' ring. After a number of nose wheel compression cycles the strut will
become flat and knock against the wheel even when taxiing. Every subsequent
landing causes the shock of the nose wheel landing to be transmitted into the
firewall and the engine mounting. Now, the damage is not just to the gear but in
the engine and the aircraft airframe. I recently (February '94)saw someone
taking the NRI 172 and make somewhere between 4 and 6 touch-and-go's. Every one
of the 'landings' was flat. Not once was the nose wheel held off the runway for
even a moment.
Not long before that I saw four people get into the C-172. I questioned the
pilot regarding weight and he said that he was in limits. When the heavy-weight
of the group got into the back seat, I again approached the pilot and suggested
that balance might be a problem. Is there a problem or is Gene Whitt making one?
Saw the same thing in Hayward yesterday 11-14-98.
What can be done? First, I don't believe anyone deliberately, and knowingly
damages an aircraft or exposes passengers to danger. A pilot may have erroneous
perceptions as to what makes a good landing. Maybe, there is a problem with
knowing aircraft attitudes. Is establishing a stabilized approach at a constant
airspeed the problem? Very possibly, it is caused by a situation beyond the
pilot's experience. Consider.
A single pilot in a C-172 with his seat well forward. The C-172 has a full radio
stack. The aircraft is within C.G. limits. A final approach at 60 knots will
give the elevators enough authority to round out. As the aircraft decelerates
below 60 knots the elevator loses authority and may well be unable to raise the
nose even if full back and up. This is especially true if the power has been
taken off.
Under these conditions, what should the pilot do? If you can't arrange to get
one passenger in the back seat, you should plan to leave at least 1200 rpm. The
power will help hold the nose up and give the elevator the authority required
for a full stall landing. Very careful energy management will be required to
avoid a balloon. It can be done to a full stall landing every time. You will not
be able to see the runway. The nose wheel will remain well clear of the ground.
Power can be applied for the takeoff and the flaps removed without the nose
wheel ever touching the ground. Alternatively, the power can be taken off as the
nose wheel touches.
If the C-172 is fully equipped with radios and panel gear, a full stall landing
may vary from difficult to impossible depending on the seat position of the
pilot. Landing with power at 12-1300 rpm as in a soft-field landing will make
full stall landings easier. The C-172 lands better with a rear seat passenger.
Since CCR refuelling practices avoiding fuel overflow, be sure to make an
allowance for less than full tanks. A fuel tank will not hold as much useful
fuel on a hot day.
A C-172 at a density altitude of 11,000' and properly leaned will only develop
98 horsepower instead of its 160 at sea level. We now have a C-172 attempting to
takeoff with a C-150 engine. This is not a takeoff situation even leaned and
suicidal with a rich mixture. With a rich mixture you would be pumping over 10
gallons an hour of fuel into a engine which for best power should only have 7
gallons per hour. You lose from an overly rich mixture in many ways. Wings and
propeller cannot be turbocharged so their capability cannot be changed. CCR
density altitude at 100 degrees F is 3000'. Plan and fly accordingly.
Top of page

Exercise in C-172:
Go to slow-cruise of 90 knots and reset the attitude indicator for
level. Cover the AI. Initiate a climb with full power and confirm that the climb
is reasonable both in attitude and airspeed. Reduce power for slow-cruise and
make a 15 second right standard turn. Level off and initiate a descent by
reducing power. Level off by adding power. Make a 15 second turn to the left. Do
this several times to develop a sense of control and safety. You will learn that
attitude plus power gives performance. The had move in unison on the yoke and
throttle to give the desired performance. From this proceed to develop the
attitudes and power required to give you all the performance parameters required
for all performance situations. You want to learn to control the airplane so
that flying is not a part of the instrument flying equation. There is no one way
to initiate, perform, and conclude a given manoeuvre. The following procedures
are merely suggestive as one way.
Top of page

C-172 Procedures and Landings
1. Abeam numbers, power back to 1,700rpm. Hold the heading and altitude.
2. Decelerate and trim for 70 knots.
3. 10 degrees of flaps, trim for 70 knots
4. 20 degrees of flaps on base. Trim for 70 knots
5. Turn final, flaps as required, trim for 60 knots.
6. Use power as the variable to control arrival.
7, Use rudder/ailerons to align with runway
8. Make small pitch corrections in the roundout.
9. Flair as the numbers go under your nose.
10.Keep holding a little back pressure
11.When you feel the plane starting to settle, raise the nose to cover the far
end of the runway.
Top of page

Precision Approach Speed No Flaps
Clearing turns
carburettor heat
Power to 1500
Hold altitude with yoke
Trim down as far as it will go
Power to 1800 for minimum controllable at 50 knots
Power to 2000 for slow flight @ 60 knots
Top of page

Level Cruise
Full power until 100 knots
Power to 2450
Trim
Top of page

Climb at 90 Knots
From level cruise
Raise nose to climb attitude
full power
One+ trim down.
Fine trim for airspeed
Top of page

Level Approach Speed at 90 Knots
From level cruise
Power to 2200
One+ trim up
Top of page

Level Approach Speed at 90
Knots #2
From Climb
Lower nose
Lower nose to level
At 90 knots reduce power to 2200
Fine trim
Top of page

Descending Approach Speed at
90 Knots
From climb
Reduce power to 2000
Lower nose to descent attitude
Fine trim for airspeed
Top of page

Approach Descent Speed at 90
Knots
From level approach speed
Power to 20000
Fine trim
Top of page

Slips with Flaps
POHs 172
The owners manual for the 1967 Cessna 172 states on page 2-11
Normal landings are made power-off with any flap setting. Slips are
prohibited in full flap approaches
because of a downward pitch encountered under certain combinations of airspeed
and sideslip angle.
The 1976 POH requires a placard which states "AVOID SLIPS WITH FLAPS EXTENDED"
Landing section for Normal landings states:
"Steep slips should be avoided with flap settings greater than 20 (degrees) due
to a slight tendency for the
elevator to oscillate under certain combinations of airspeed, sideslip angle,
and centre of gravity loadings."
"The maximum allowable crosswind velocity is dependent upon pilot capability
rather than airplane
limitations. With average pilot technique, direct crosswinds of 15 MPH can be
handled with safety." No
max demonstrated crosswind speed is in the POH. The 1967 model has 40 degrees of
flaps available.
The 1970 (C172K) model's POH (1970 model also had 40° flaps) has been
changed to read "Slips should be avoided with flap settings greater than 30°
..." No required placard is noted in the Limitations section.
Placards are required by model:
According to the TCDS 3A12 (covering models 172 - 172S), regarding slips, the
following On flap handle,
Models 172 through 172E:
"Avoid slips with flaps down."
Near flap indicator Models 172F (electric flaps) through 17271034, excluding
17270050):
"Avoid slips with flaps extended."
The 172 manuals suggest, but do
not restrict, not slipping the aircraft with more than 20 degrees of flaps. On
that model doing so would occasionally induce "elevator oscillations." No such
notation appears in the 182 POH, or the POH of any other model Cessna besides
the 172, because no such elevator oscillations have shown up in full flap slips
on other models. Probably has something to do with different fuselage lengths
and tail sizes. Having intentionally gotten a 172 in this configuration in my
flight instructor days, I did after much effort, get some elevator oscillation.
No big deal, just some momentary change in stick force at the control wheel.
Plane remains fully controllable, however, I can see where it would be
disconcerting for the pilot, particularly if it occurred during the landing
flare. But again this only applies to the 172.
Top of page

Landing Problem (Opinion)
I had the plane trimmed for landing, and I was seemingly pulling with all my
might to flare. Is this normal?
I've got about 800 hours in a 177B and a 177RG and I'm a bit puzzled by your
problem with high flare forces. The main difference between the Cardinals and
other Cessna trainers is the stabilator. At high speeds, trying to overpower the
stabilator if it's out of trim will require huge yoke forces, but at flare
speeds it gets much lighter. My thought is that you were coming in hotter than
you may have realized and that the plane was not trimmed quite right. I find
that if I get the plane slowed down to 90ish KIAS and level in downwind with
10-degrees of flaps out, and get a decent trim setting for that configuration,
then the plane will almost fly itself down through the rest of the pattern
through a power reduction and subsequent additions to flaps, with only minor
trim adjustments required.
So theory 1 is that you were actually too fast on final and not really trimmed
right.
Theory 2 is almost the opposite: you were trying to impress your instructor by
flying a nice slow short-field approach with 30-degree flaps. You were in a
significant nose-down angle and tried to pull it up at flare to the stalling
pitch all in one fell swoop at minimum airspeed, just as the stabilator is
losing the last of its power. The yoke is in fact very light in forces, but
you're actually so tense trying to horse the heavy nose from its steep nose-down
to a stalling nose-high pitch in two seconds that you've got the yoke against
the stops, which feel darn heavy :-)
Theory 3 is that the stabilator bearings, cable pulleys, or antiservo tab on the
stab need maintenance; it does sometimes happen that things do wear out in only
three decades :-) (As a side note, all early Cardinals were "recalled" to get
the stabilator slot mod mentioned by another poster, so that's really only an
historical curiosity.)
Anyway, my suggestions are:
(1) Trim it out nicely on downwind, when you've got your speed stabilized at
85-90KIAS or so.
(2) Initially work on landings with 20 degrees of flaps. This doesn't get the
nose as far down, so makes for an easier transition to nose-high landing
attitude.
(3) Watch your airspeed like a hawk on final until you're 10-20 feet AGL.I
suspect it's easier to pick up a little too much airspeed on short final in the
177 than the 15X you're used to. Conversely, if you get too slow, the 177 will
sink pretty fast even if you're not near stall. I like 65-70KIAS on final with
the FG, about 5 more for the RG. You'll have to adjust these speeds to MPH if
you've got a pre-1976 Cardinal. Work on the slower short-field approach after
you're happen with the normal landings.
(4) If you can't take your hand off the yoke and fly with the rudder any time
during a straight segment of base or final, the trim, power, and airspeed must
not be right. It should be two fingers' yoke pressure until the flare.
(5) Make a distinct separation of the roundout and flare. For the roundout, pull
up just enough to break the glide and fly the plane level down the runway at a
height you're not afraid to fall from, somewhere between one and six feet
depending on how good your depth perception is. Lower is better, as long as you
don't whack the nosewheel first, but don't worry too much about being a little
high as long as the stall horn isn't tormenting you. Freeze your stabilator
pullback position to fly flat until the plane slows. You should have all the
power eased off no later than breaking the glide unless you are attempting an
honest-to-God soft field landing, and probably even then.
(6) Wait for the plane to slow and start sinking before you pull back any more.
As the plane sinks, ease in more up-stabilator to try to keep the plane at the
roundout height. When the plane gets tired of flying, it will land on the main
gear, which is the whole point. Drop the nose gear whenever you like. Voila!
You've flared and landed. The stall horn may or may not be busy at this time,
depending on how high you want to point the nose. As long as you touch down on
the main gear first on a paved runway, it's mainly a matter of taste.
Some people like to dial a bunch of nose-up trim for flaring; I don't touch it
after entering short final and usually it ends up close to the take-off trim
setting, fairly neutral for around 70 KIAS. As another person mentioned, if you
do use a lot of up trim, be prepared to demonstrate some good tricep muscle on a
go-around. You'll have to do it one handed too, since the other hand will be
spinning the trim wheel like a top :-) I prefer a neutral setting, but it's a
matter of taste.
Once you've broken the glide and stabilized the plane level above the runway,
NEVER EVER PUSH THE YOKE FORWARD. If you have pitched the nose too far up and
it's ballooning up, GO AROUND and do better the next time, don't push it down
like you can get away with in a 172. The nose is heavy and the stabilator is big
and powerful and if you get the two working the same way you can do amazing
things to the nose gear, none good, as you porpoise down the runway. If you've
got it up just a little too much, freeze the yoke back-position (it's still fair
to use your ailerons, of course), and wait for the plane to slow down and
settle. I slammed plenty of 172s into the ground as a student pilot, and I
honestly think the Cardinal is an easier plane to land once I got the trim and
airspeed calibrated on final and abandoned my old 172 flare technique of yanking
the elevator back to the chest in one swift motion as soon as I saw the
instructor tense up and start to reach for the yoke.
As you get more experience with the plane, it will be easier to blend the
roundout and the flare together, but even now if landing conditions are
marginal, e.g., gusty winds, I will round out and fly the plane a few feet above
the runway to make sure I'm happy that things are under control before
committing to the flare and landing.
I hope you find these suggestions helpful. I think the Cardinal is a great plane
(though a turbo and/or another (fillintheblank) HP would be nice too) and a
decent cross-country vehicle. And if you get a few more hours and still think
the yoke forces are superhuman, maybe somebody should look the stabilator
mechanicals over. One of the major problems with Cardinals is that there are
more than a few mechanics who think that everything put in a 177 must be just
like a 1X2, so why look at the service manual? You could buy out Bill Gates with
the money that's been spent to replace FG shimmy dampeners that have exploded
after getting topped off with fluid, ala 172s. :-( Luckily, that's only fatal to
wallets, not pilots.
Top of page

Second Opinion
The 172 is not easier to land -- it is different. It has a distinctive
tendency to balloon if your approach speeds are too high. The greater weight
gives a more solid feel to the plane, but to be honest I really don't think
there is all that much practical difference between the two planes.
The 152 is not dangerous in spins. A few hysterical chicken littles, notably on
this ng, have gone overboard on a 152 in Canada that crashed during a spin. This
152 was missing several parts that had been removed by a mechanic who didn't
think they were important. Inspection of other 152s at that same school revealed
that most of them were missing the same parts (what a surprise). This mechanic
had worked on 152s elsewhere and they had been similarly modified -- so the
Canadians issued an AD requiring all the 152s in the country be checked. The FAA
in the USA works the same way. If someone cuts their finger, everyone has to
take their fingers in to be checked to see if they are bleeding.
The 152 is probably one of the safest aircraft in the world when it comes to
spins. It would be hard to argue that the 172 is any better. In any event, spins
are the least of the problem if you are looking at the relative safety of a type
of airplane. Both the 152 and the 172 have a long list of airworthiness
directives. Most of these directives were probably issued as a result of a fatal
accident. Yet these planes have a fatal accident rate per 100,000 hours that
rivals that of airliners.
The 172 is a lot less tolerant of overloading than the 152. The small Cessnas in
general have a large envelope, but it is possible to get them out of balance
with just two people in front. The bigger the Cessna the worse the problem seems
to be until in the 206 people take to loading weights in the back to keep the cg
in limits.
Of total accidents both fatal and nonfatal caused by a stall (including spins),
the 172 has almost the best rate of any plane, with 0.77 accidents per 100,000
hours. The 150/152 is about twice that at 1.42; still very good when you
consider that both these planes are used extensively as trainers. Considering
the people who fly them, the 152 does very well indeed, as does the Tomahawk and
other 2 seat trainers of the period. They were a tremendous improvement over the
Cubs which had accident rates that were more than five times greater. All the
planes that are better than the 172 are also Cessnas, except for the Bellanca
14-19 and the Piper PA-32. The plane with the best record in stalls is the
Cessna 182 at only 0.36 accidents caused by stalls per 100,000 hours, followed
by the 195 at 0.47 and the 206 at 0.54. Compare this to the Aeronca 7's rate of
22.47 and a rate of around 5.0 for most Piper taildraggers.
Both the 150/152 and the 172 generally are near the top of the class in any
category of accident, whether engine or airframe failure or bounced landing. The
172 probably has the best safety record of any general aviation plane ever
built, but the 152 and the Piper PA-28 are not far behind. When these planes do
have accidents their fatality rate is exceptionally low. The huge majority of
accidents in these planes are simple fender bender types, with a good sprinkling
of botched landings -- these planes are trainers after all.
Many people believe that trainer aircraft such as the 152, the 172, the PA-28,
the PA-38, etc., were made deliberately hard to fly in order to make better
pilots. I would like to see some evidence of this. These planes are so easy to
fly that they have made pilots of many people who would never have otherwise
been able to fly. Until these planes were introduced only an elite few had the
talent necessary to make the cut. They put flying in reach of everyone, and for
awhile up through the 1970s it looked like aviation had reached a critical point
where someday learning to be a pilot would be an expected skill of everyone,
like driving a car. Many factors conspired to end that dream, and the number of
pilots being produced today is only a fraction of what we once turned out. Our
numbers are increasing, but it will probably be many years before we return to
anything like those days.
Top of page

Fuel
Problems of Cessnas
Significant fuel imbalance has been
explained away as due to overflow venting pipes being pressurized by air
in flight. However, it has been found to be due to fuel tank sealant obstructing
fuel tank vent lines as well.
See Cessna service bulletin SEB 99-18
Top of page

C-172R Data Sheet
Vso
33
Vs 44
Vfe 30°
85
VFE 10°
110
Va
2450 lb
99
Va
2000 lb
92
Vno 123
Vne 163
Vr 55
Vx 60
Vy 70
Climb 85
Short field T/O
- flaps 10°
- slightly tail low
- init climb at 57
Max Glide
65
Landing
No flaps
70
30° flaps
65
Short Field
62
Lycoming IO-360, 160 hp @ 2400
Fuel: 100 or 100LL, 56 tot, 53 gal usable, 35 gal at tabs
Oil: 6 to 8 qt
Power settings TAS GPH
Take off FT/2400
Cruise climb 2400# 85 11.0
4000 ft 79% 2300 117 9.1
66% 2200 111 8.1
6000 ft 80% 2350 120 9.2
71% 2250 114 8.1
8000 ft 80% FT/2400 122 9.2
76% 2300 116 8.2
10000 ft 72% FT 118 8.2
12000 ft 69% FT 117 7.9
Lean 50°F rich of peak EGT
Approach
Clean 2100 90 level
10° flaps 2300 90 level
(precision desc) 1900 90 500 fpm
(non-precision) 1500 90 1000 fpm
In pattern clean 1900 85 level
Top of page

A Better Way to Move a 172
Now that we are encouraging members
to push the plane to and from the fuel and pre-heating stations to save starting
wear and tear, we need an easier way to move it for the solo pilot. Even if you
don't have arthritis in your hips, struggling with the too short tow bar is a
pain. This method works the nuts.
There are now two 48" long loops
of 3/16" bungee cord on the towbar handle and a length of rope. Put the towbar
on backwards, hook the loops around the step on the landing gear, and run the
run the rope over to the other side where you push on the strut. Pull to steer
one way, release to steer the other. Tight turns are only possible in one
direction so think ahead which side you want the bungee on.
This setup works even better in
reverse because you aren't working against the trail of the gear. You can back
the plane precisely into the tie down from out to the side where you can see. As
a bonus, the tension of the bungee keeps the towbar from popping off.
The geometry just happens to
work our for our tie down such that the plane will track right towards the
pre-heating spot with no steering required if you put the bungee on the
passenger side. A slight pull when you get close to the hanger and, you are
there. There is a spare bungee in the milk crate.
Cessan
vs Piper
--Seat belt systems are somewhat different.
--Flap relationship to trim is unique one from the other.
--Best to have your own POH for every aircraft you fly.
--Most of the checklist items will have a different sequence
--The first item of your emergency checklist will be different.
--Manufacturer's instructions related to carburettor heat differ.
--Night and cockpit lighting systems require distinctive explanations.
--The manoeuvring and taxiing blind spots are usually quite different.
--One door system is more likely to accidentally open as the other is.
--Cross wind and ground handling in strong winds distinctly different.
--One flap system is more controllable and consistent than the other is.
--Seat adjustment systems are just different enough to cause difficulties.
--Never plan to immediately fly hard IFR in a newly transitional aircraft.
--The way you hold your hands on the throttle should be quite different
--One fuel system is twice as likely to cause an engine failure as the other is.
--POH numbers and explanations vary year to year and even within the
year.
--You should always make your own aircraft specific operational checklist.
--Confirm the 'neutral' position of the trim setting indicator with actual
trim position.
--Learn all you can about the failure modes of all unfamiliar instruments in
either type.
--Gear retraction and extension of one is less likely to give problems than the
other is.
--The way you use the rudder pedals and brakes have a VERY dangerous difference.
--The preflights are distinctly different with differing critical points where
mistakes occur.
--Get some pre-flight cockpit time for reading the POH and referencing the
cockpit to it.
--Run the trim wheel all the way up and down, manually and electrically to
become familiar.
--Within the same models of each manufacturer there are wide critical airspeed
differences.
--Both manufacturers have made wing, elevator and instrument changes affecting
critical speeds.
--Distinct differences in handling when at gross and near either end of the
center of gravity range.
--With two exceptions, one type is more likely to have a stall/mush accident in
all its models than the other is.
Top of page

Aircraft Proficiency Checkout
Preflight
Removal and storage of cover
Checking time log/pitot cover and control lock storage
Cargo doors not to be slammed.
Refuelling procedures
Location of POH/weight/ balance and aircraft papers.
Cockpit lighting
Starting procedures
Priming without throttle
Prop-wash effects behind
Detecting carburettor ice
Taxi procedures
Mixture leaning
Power vs brakes
Controls set for wind direction
Run-up
Facing wind or local requirements
Use of hand brake/foot brakes
Magneto check drop comparison
Clearing fouled plugs
Pre takeoff
Clearing the bases and final
Confirming power available
First power reduction at 1000'
Levelling off
Allow acceleration before power reduction|
Setting 75%, rpm and leaning
Trim and use of auto pilot (Operation and failure modes)
Heading and altitude control
Coordination of flight
Radio Procedures
Initial call to ATC and follow-up
Non-tower airport operations (Pattern operations)
Light systems
Manoeuvre
Steep turns
Slow flight
Stall recognition/recovery
Emergency procedures
Simulated engine failure
3 take offs and landings to include
No flap
Short approach
Short and Soft
Full flap go-around
Top of page

Modified C-172s
The modified C-172 with power flow exhaust systems have sufficient power
to surprise the pilot and reach this stall before being corrected. Do NOT trim
for the flare as a safety measure. The go-around performed with trim applied
for the flare can be deadly.
The C-172 rudder was originally
designed for a 145 engine. With a 180 engine and a power flow exhaust system
you are getting 200 hp. This aircraft in flare and power applications will
require considerable rudder. It does not pay to be rudder-lazy in a modified
C-172.
Top of page

1963 C-172 Suggestions
If the C-172 has a stock 150h.p.
Lycoming it is more underpowered for its weight than a C-150. This means that
when reaching pattern altitude you must stay at full power for a considerable
time for the aircaft to accelerate before reducing power. (Alternative is to
climb 100' high and dive to reach cruise speed more quickly.) Suggest that you
go to altitude and have students practice climbs of 500' to level cruise several
times with the intent to reduce the amount of time it takes to be hands-off
level cruise.
If the final approach speed is
to be 1500 rpm, teach them to reduce power to 1700 abeam the numbers, Since this
done at cruise speed the momentum of the plane will initially drive the prop
before it slows to the desired 1500. Trim down three times using fingertip
behind top button to pushing that button into bottom slot. Doing this will, if
student holds heading and altitude, allow the plane to extend the downwind just
the amount required for turning base at 80 mph. Put in the first ten degrees of
flap and take off one finger-tip turn of flap as plane descends at 70 mph. Check
with hands off controls. Turn base.
On base put in 20-degrees of
flap and take off another turn of trim. Change base angle to adjust sense of
high or low for turn to final. Turn final and put in full flaps. No change in
trim required. (Aircraft will be trimmed for Vy go around speed when flaps
removed.) Approach speed will be 60 mph hands off.
Individual aircraft will vary
this procedure but not by much. Back seat passengers will make significant
change in yoke pressure required for landing flare. Still I suggest you do all
lessons with two students and recorders (See my site) With due care you can
change student seats in the air at altitude. Practice on the ground. This will
allow one student to watch a lesson and apply it to his lesson.
Note that the 1963 wing does not
have the 'cup' that later models have. Presume your flaps are non-electric.
Makes for great landings and flight path control. Great year, great airplane.
You may find that solo students of light weight are unable to get the nose up at
60 mph. Try, as I did, a sack of cement in the luggage compartment.
|