power turbine
The turbine has the task of
providing power to drive the compressor and accessories. It
does this by extracting energy from the hot gases released
from the combustion system and expanding them to a lower
pressure and temperature. The continuous flow of gas to which
the turbine is exposed may enter the turbine at a temperature
between 850 and 1700 °C which is far above the melting point
of current materials technology.
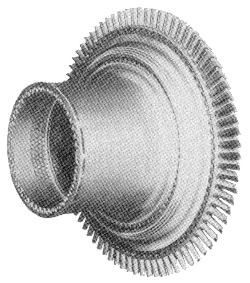
A high-pressure turbine
stage from a CFM56 turbofan engine
To produce the driving torque,
the turbine may consist of several stages, each employing one
row of stationary guide vanes, and one row of moving blades.
The number of stages depends on the relationship between the
power required from the gas flow, the rotational speed at
which it must be produced, and the diameter of turbine
permitted. The design of the nozzle guide vanes and turbine
blade passages is broadly based on aerodynamic considerations,
and to obtain optimum efficiency, compatible with compressor
and combustor design, the nozzle guide vanes and turbine
blades are of a basic aerofoil shape.
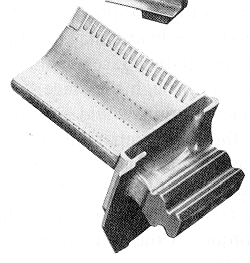
A turbine blade with
cooling holes
The desire to produce a high engine efficiency demands a high
turbine inlet temperature, but this causes problems as the
turbine blades would be required to perform and survive long
operating periods at temperatures above their melting point.
These blades, while glowing red-hot, must be strong enough to
carry the centrifugal loads due to rotation at high speed.
To operate under these conditions, cool air is forced out of
many small holes in the blade. This air remains close to the
blade, preventing it from melting, but not detracting
significantly from the engine's overall performance. Nickel
alloys are used to construct the turbine blades and the nozzle
guide vanes because these materials demonstrate good
properties at high temperatures.
|