A fully restored
Meyers 200A
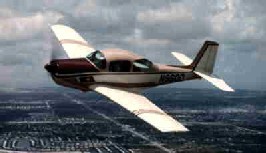
The Meyers 200D - 4 place, fully enclosed
retractable gear
Continental IO-520 engine
In
1974, Al was elected to the Pioneer Aviation
Hall of Fame. The Meyers 200 series aircraft
have never had a FAA mandated Airworthiness
Directive (AD) issued against their
airframe, something no other aircraft can
claim. It was, and still is, regarded as
perhaps the finest single engine production
aircraft ever built. There are currently 102
Meyers 200 type aircraft registered in the
U.S. today.
The Meyers 200D set many speed records
during the 1960's. Peter Gluckman set a
class around the world record with a Meyers
200D equipped with auxiliary fuel tanks.
Jerry Mock, a Columbus, Ohio, homemaker, set
several records in Women's racing in the
Meyers 200D. She piloted a 200D to a new
world speed record for 500 kilometres in
Class C-1b. Her average speed of
203.858 mph broke the ten year old record of
178 mph set by a Czech racing plane. Bill
Brodbeck set a National Aeronautic
Association (NAA) speed record of 227.24 mph
in Class C-1b over a 3 km course which stood
for almost eighteen years. Bill also set a
Federation Aeronautique Internacional (FAI)
World record of 365.700 kmh. Then Don
Washburn, flying a standard production 200D,
claimed a record of 239.5 mph (208.26 kts!!)
in class C-1c over a 3 km course. The
Meyers is the fastest, normally-aspirated
(non-turbocharged) production piston single
engine plane ever built. The Meyers 200D is
faster than even the fabled Piper Comanche
400 which has 400 horsepower. Many magazine
articles have been written about the Meyers
200D.
Safety
Record
The Meyers 200D
has never had an in-flight structural
failure and has never had a FAA mandated
Airworthiness Directive (AD) issued against
the airframe. The 4130 chrome-moly steel
tubular roll cage and understructure act
like a race car protective cage during a
crash. Several Meyers aircraft have been
forced down in the trees and off airport
runways with documented instances of the
occupants walking away with only minor
injuries or a broken bone.
Rockwell
The North
American Rockwell Corporation (now Rockwell
International), through its Aero Commander
Division, was attempting to build a large
aviation conglomerate. Rockwell approached
Al Meyers to purchase the Meyers 145 and
Meyers 200D Type Certificates. They reached
an agreement and consummated the
transaction. The Meyers aircraft were
basically hand built from the very
beginning. The rudimentary jigs and fixtures
that existed were actually hung from rafters
in their small facility, consisting of maybe
10,000 square feet. When no aircraft was in
production, the jigs were pulled up into the
rafters and the workers were busy repairing
aircraft. When Meyers received an order, the
jigs were lowered and the plant went into
production. A very small number of highly
skilled craftsmen, many of whom had been
with Al Meyers from the beginning, hand
constructed each aircraft. Hard production
tooling, the kind that allows semiskilled
workers to build aircraft, simply did not
exist. The only tooling that did exist were
some wooden and cardboard templates hanging
on the walls, the simple final positioning
jigs and fixtures and the hand notebooks of
the workers involved. These workers had
built various parts of the aircraft for
years; thus little tooling was really needed
to turn out a completed aircraft.
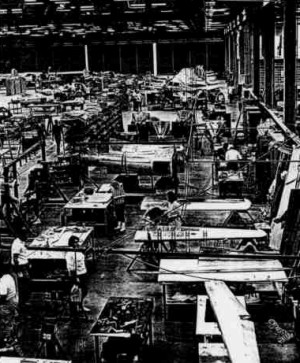
photo of 200D production line in Albany,
Georgia
Since no production tooling existed,
Rockwell had to create all of the tooling
that Meyers Aircraft now possesses,
virtually from scratch. Paul Nichols, the
production test pilot for Rockwell's Albany
Division and who now works for Ayers
Aircraft, who purchased the facility from
Rockwell, has advised he has seen reports to
Aero Commander's Corporate Headquarters
indicating that it was taking over 10,000
man hours to build each Meyers 200D.
Analyzing other industry reported averages,
it is now known that the man hours should
have been in the range of 2000 to 2500
hours.
It
seems clear the Rockwell plant personnel
were including the hours necessary to create
all of the non-existent tooling in the hours
they were reporting for each aircraft.
Rockwell Corporate decided that it could
never make a profit with an aircraft that
took 10,000 hours to build so it decided to
turn its design team loose on a single
engine project that it hoped would be easy
to produce. Thus was born the Commander 112.
The Commander 112 turned into the 114B which
remains in limited production in Norman,
Oklahoma.
Management has spent considerable time and
effort reconstructing the events that lead
up to this decision by Rockwell to cease
production of the Meyers 200D. The 112 was a
far inferior aircraft and very slow compared
to the Meyers 200D. It has also had numerous
severe Airworthiness Directives (ADs) issued
against key structural components that have
even grounded the entire fleet. Paul
Whetstone has compared the manufacturing
time against industry reported times and the
DAPCA IV Development Cost and Production
Model. The high end is around 3,000 hours
and through production familiarization, goes
down to below 2,000 hours. It is now quite
evident that the 10,000 hours reported to
Rockwell Corporate were mis-categorized,
causing it to make one of the great
misguided decisions in light aircraft
production history. Because of Rockwell's
mistake, Meyers Aircraft now has the
opportunity to produce and market the
"...best Airplane Ever Built...", sell it
for more than $100,000 below the
competition, and yet maintain an industry
standard profit.
Interceptor Corporation
During the time that Rockwell was deciding
to stop production of the Aero Commander
(Meyers) 200D, they were approached by Lymon
Lyon of Detroit. Lyon had dual degrees, one
in mechanical engineering and the other in
law. Lyon had flown behind turboprop power
in the military and decided that he wanted a
personal turboprop. He researched the market
and decided that the Aero Commander (Meyers)
200D had the strongest airframe in
production and approached Aero Commander to
build one for him with a turboprop engine.
Aero Commander told him that it was in the
process of ceasing production of the Aero
Commander (Meyers) 200D and suggested that
he purchase the Type Certificate (TC) and do
it for himself.
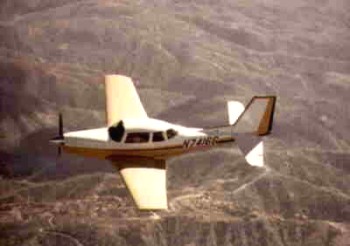
Interceptor 400
as certified in 1971
Lyon then formed the Interceptor Corporation
with a group of physician investors from the
Detroit area. They chose Don Long, a senior
project engineer with Aero Commander to head
up the Company. Long had been responsible
for the certification of the Jet Commander.
He estimated that it would take six months
and $600,000 to certify the turbine engine
single.
In
reality, it took almost three years and
several million dollars. Nevertheless, the
Interceptor 400 was certified in 1971 and
added to the TC as the Model 400.
As
the "hot" new aircraft of the early
seventies, the Interceptor 400 was involved
in a 20+ year "great debate" in the aviation
industry over which is safer, a single
engine aircraft or a light twin engine
aircraft. Dozens of articles have been
written on this subject. Most of the major
manufacturers were pushing for twins because
they made more money on a twin than on a
single. The Interceptor 400, as the first
turbine single to be certified in the U.S.,
was a major factor in the "single" camp.
History has shown that timing is everything
when it comes to the introduction of a
revolutionary product. Hindsight shows that
it is just as fatal to be too early as too
late. At that time, the pilot community was
not ready to accept turbine engine singles.
The argument has now been largely resolved
in favour of the turbine single-engine
aircraft. In the last few years, several
turbine singles have appeared and have been
publicly accepted. Cessna, through its
single-engine Caravan used by FedEx, was the
major factor in changing the industry
conception. Then came the Socata TBM-700 and
the Pilatus PC-12. Piper announced the
development of the Malibu Meridian.
Just this year, the FAA has stated that it
will remove the prohibition on single
turbine-engine Part 135 Air Taxi flights.
The decision makers have really been the
insurance companies who charge more to
insure a $100,000 hull value twin than a
$100,000 hull value single. A 1993 quotation
from AVEMCO showed that the same hull value
Saratoga single would cost $1978 whereas the
Seneca twin would cost $2576. When safety is
coupled with the vastly greater reliability
of the prop-jet engine, the Interceptor 400
is one of the safest aircraft in the sky, as
is the piston powered Meyers 200D.
An attempt to continue production was made
by the Seminole Native Americans under the
name of Micco. MICCO Aircraft Company did
finish the certification of the 200hp SP20
and the 260hp SP26 and then took the SP26
through aerobatic certification.
The enterprise was marred by a series of
lawsuits and internal politics and what
appears to be very bitter and aggressive people.
The company delivered 16 aircraft, eight
SP20's and eight SP26's and had 26 orders on
hand when the political trouble started and
the company was sold.