
air
injection
starter
In limited use at the present time, the air injection starter
has been developed as a light-weight and efficient starting
means for aircraft engines rated up to 250 horsepower.
Operated from self generated air pressure, this type of
starter was particularly suitable for application on engines
of small output where an electrical installation was not
possible and manual hand-cranking undesirable and inadequate.
The Air injection starter equipment
consisted of a small and compact engine-driven air compressor,
a timed rotating distributing valve, integral with the
compressor, a tubular air storage tank, an automatic pressure.
regulating valve, pressure release starting valve, and an
instrument panel mounted pressure gauge and primer. However,
as the majority of light powered airplanes at the present time
are equipped with engines designed to accommodate a generator
of low output, the direct cranking electric type of starter is
replacing the majority of air injection starter installations
due to its light weight, simplified installation, and freedom
from service troubles. Due to the extensive plumbing required,
and the corresponding possibility of air leakage in the
system, the air injection type of starter is only recommended
for installations where battery and generator are not
available. Although primarily confined to use on engines rated
up to 250 horsepower, a starter employing this principle of
operation is widely used on foreign aircraft for starting
aircraft engines of all capacities.
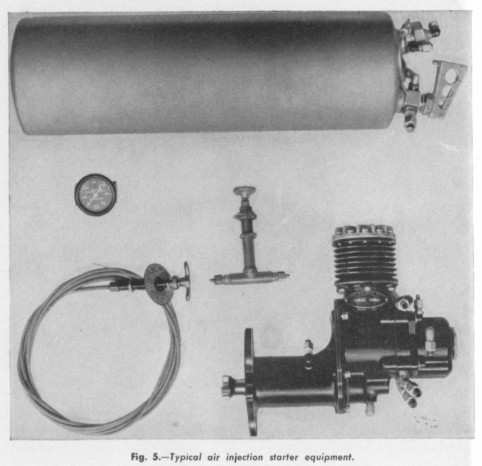
The principle of operation of the air
injection starter is as follows: The engine is cranked from an
initial air pressure of approximately 450 pounds per square
inch, which is contained in a storage tank. Release of the
compressed air is controlled from the pilot's compartment and
is transmitted by a distributor valve to the cylinders in the
proper cyclic order, thus rotating the engine. A portion of
the compressed air, in passing through the distributing valve,
forces liquid fuel into the cylinders on the compression
stroke. This carburettor priming charge is followed by a
greater volume of air which rotates the engine and assures
instant firing. The air pressure dissipated in starting is
replenished by the compressor shortly after the engine has
been started. As the maximum operating pressure of 450 pounds
per square inch is reached, the pressure regulating valve,
which is an integral part of the storage tank, automatically
stops further charging of the storage tank, thus the
compressor, driven direct from the main aircraft engine, is
temporarily relieved of pumping against pressure and rotates
freely under no load until further dissipation of the air
pressure by- starting occurs. Due to the variations which are
encountered in different installation, no definite performance
data can be given, however, under normal conditions,
approximately 20 to 30 starts can be obtained from one fully
charged tank of air without replenishment in the meantime.
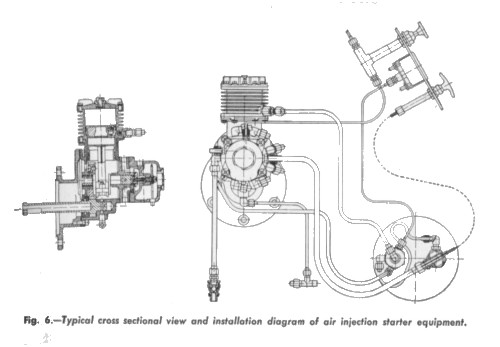
Later Developments
Of more recent application in this country is the hand or
combination hand and electric inertia starters, which have
been designed primarily for use by the military services and
are suitable for installation on engines rated up to 2,000
horsepower. The starters are particularly suited for
installations where dependability and provisions for emergency
hand-cranking are required. The basic design of all inertia
starters consists of the storage of energy in a small flywheel
by accelerating it to a high speed either manually or
electrically. The energy thus stored is expended in rotating
the engine crankshaft. Transmittal of the kinetic energy of
the rotating flywheel to the engine is accomplished through
reduction gearing, a multiple disc clutch, an engaging
mechanism, and driving jaw.
|