
aircraft engine
history
jet
engines

A
simplified view of how a jet engine works.
Before World War II, in 1939, jet engines existed only as
laboratory items for test. But at the end of the war, in 1945,
it was clear that the future of aviation lay with jets. The
new engines gave great power and thrust, but were compact in
size. They also were simple in their overall layout.
A
jet engine, down to the present day, pulls in air by using a
compressor. It looks like a short length of an ear of
corn, but instead of corn kernels, the compressor is studded
with numerous small blades. The compressor rotates rapidly,
compressing the air.
The compressed air flows into a combustor. Here fuel is
injected, mixed with this air, and burned. This heats the air
to a high temperature. The hot, high-pressure air then passes
through a turbine, forcing it to spin rapidly. The
turbine draws power from this hot airflow. A long shaft
connects the turbine and compressor; the spinning turbine uses
its power to turn the compressor.
The jet-engine principle was known early in the twentieth
century. However, jet engines work well only at speeds of at
least several hundred miles per hour. Racing planes were the
first to reach such speeds, with a British seaplane setting a
record of 407 miles per hour (655 kilometres per hour) in 1931
and an Italian aircraft raising this record to 440 miles per
hour (708 kilometres per hour) in 1934.
A
young German physicist, Hans von Ohain, was in the forefront.
He started by working on his own at Gottingen University. He
then went to work for Ernst Heinkel, a plane builder who had a
strong interest in advanced engines. Together they crafted the
world's first jet plane, the experimental Heinkel He 178,
which first flew on August 27, 1939.
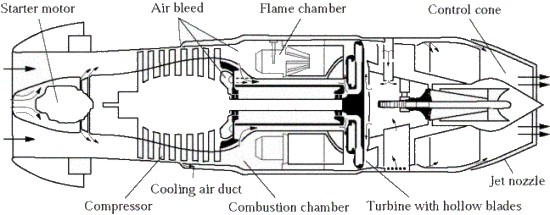
The Jumo 004 jet engine of World War II. Its main features
carried over to later engines.
Building on this work, the German engine designer Anselm Franz
developed an engine suitable for use in a jet fighter. This
airplane, the Me 262, was built by the firm of Messerschmitt.
It was the only jet fighter to fly in combat during World War
II. But the Me 262 spent most of its time on the ground
because it used too much fuel. It was a sitting duck for
Allied attacks.
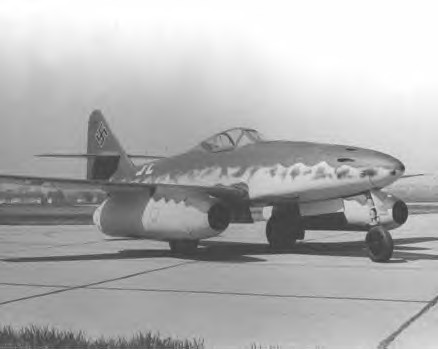
Two Jumo 004 engines powered the Me 262. This was the first
jet fighter to fly in combat and probably broke the sound
barrier first. Because the Germans had not secured a source of
chromium, the blades would stretch after a few hours making
engine life very short indeed.
In England, Frank Whittle had no knowledge of Ohain's ideas
but invented a jet engine completely on his own. The British
drew on his work and developed a successful engine for another
early jet fighter—the Gloster Meteor. Britain used it for
homeland defence but it did not see combat over Germany
because it lacked high speed.
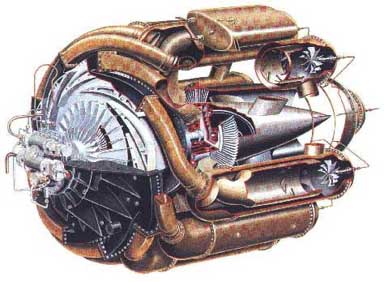
The W.1 turbojet engine used to power the
Gloster E28/39 aircraft. It was designed to produce a static
thrust of 1,240 lbs at 17,750 rpm. This engine was also the
basis of the design of the General Electric I-14 turbojet
engine used to power the Bell XP-59A twin engine experimental
fighter.
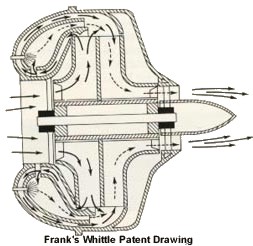
The British shared Whittle's technology with the United
States, enabling the engine-builder General Electric (GE) to
build jet engines for America's first jet fighter, the Bell
XP-59. The aircraft company Lockheed then used a British
engine in the initial version of its Lockheed P-80, America's
first operational jet fighter, which entered service soon
after the war's end. The British continued to develop new jet
engines that used Whittle's designs, with Rolls-Royce
initiating work on the Nene engine during 1944. Rolls sold
Nenes to the Soviets, and a Soviet-built version of the engine
subsequently powered the MiG-15 jet fighter that fought U.S.
fighters and bombers during the Korean War.
The surrender of Germany, in 1945, unlocked a treasure trove
of wartime discoveries and inventions. General Electric and
Pratt & Whitney, another American engine-builder, added German
lessons to those of Whittle and other British designers. Early
jet engines, such as those of the Me 262, gulped fuel rapidly.
Thus, an initial challenge involved building an engine
that could give high thrust with less fuel consumption.
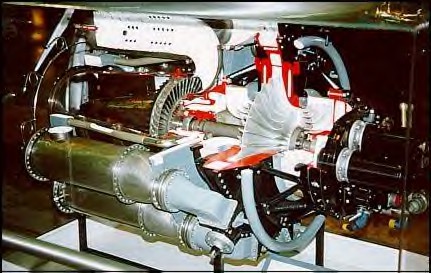
The J-31 (also known by its company designation, I-16) was the
first turbojet engine produced in quantity in the United
States. It was developed from the original American-built jet
engine, the General Electric I-A, which was a copy of the
highly secret British "Whittle" engine.
Pratt & Whitney solved this problem in 1948 with its "dual
spool" concept. This combined two engines into one. The engine
had two compressors—each rotated independently, with the inner
one giving high compression for good performance. Each
compressor drew power from its own turbine; hence there were
two turbines, one behind the other. This approach led to the
J-57 engine, which entered service with the U.S. Air Force in
1953.
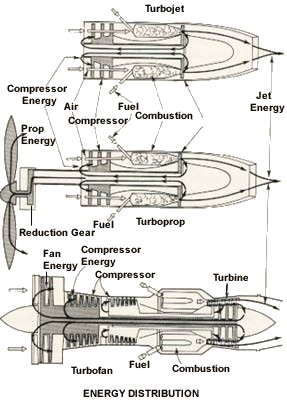
The turboprop used power from a jet engine to drive a
propeller. Additional turbines, placed near the exhaust,
tapped this power and spun rapidly. An attached shaft
delivered this power to a gearbox. Turboprops drew attention
between 1945 and 1960 but lost out because jet aircraft were
faster.
This was one of the outstanding post-war engines. It powered
U.S. Air Force fighters, including the F-100, the first to
break the sound barrier without going into a dive. Eight such
engines powered the B-52 bomber. Commercial airliners—the
Boeing 707, the Douglas DC-8—flew with it. This engine also
saw use in the U-2 spy plane, which flew over the Soviet Union
and photographed its military secrets.
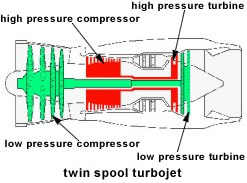
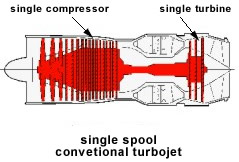
Twin-spool jet engine (top) compared with a conventional design
(below).
Note that the twin-spool version has two compressors, each
driven by its own turbine. This arrangement gave more thrust
with better fuel economy.
The dual-spool engine represented an important step forward,
but engine designers soon wanted more. As they reached for
increasing performance, they ran into the problem of
"compressor stall." This meant that at certain speeds while in
flight, the compressor would pull in more air than the rest of
the engine could swallow. Compressor stall produced a sudden
blast of air that rushed forward within the engine. The engine
lost all its thrust, while this air blast sometimes caused
severe damage by breaking off compressor blades.
During the early 1950s, Pratt & Whitney rode merrily along
with its J-57. Its competitor, GE, had a good engine of its
own: the J-47, which powered the F-86 fighter and B-47 bomber.
Still, GE's managers wanted something better. They got it from
the engineer Gerhard Neumann, who found a way to eliminate
compressor stall. Neumann introduced the "variable stator."
This was a set of small vanes that protruded into the airflow
within the compressor. Each such vane was like your hand that
you stick into the outside air when you ride in a car. Like
your hand, each vane could turn as if mounted to a wrist. When
the vanes faced the airflow with their edges forward, they
allowed the flow to pass them freely. But when the vanes were
turned to present their broad faces to the flow, they
partially blocked it. These vanes then reduced the amount of
flow that was passing through the compressor, and kept it from
gulping too much air.
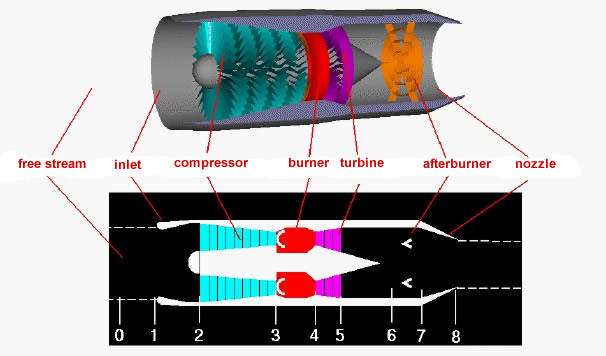
Jet fighters gained speed by burning fuel within an
afterburner. This was a tube fitted to the end of the jet
engine. Exhaust from that engine contained a great deal of hot
air and allowed fuel to burn within the afterburner, for more
thrust.
This invention led to an important GE engine, the J-79. It
became the first true engine for supersonic flight. With it,
the Lockheed F-104 fighter flew at twice the speed of sound.
In May 1958, U.S. Air Force pilots used this airplane to set a
world speed record of 1,404 miles per hour (2,260 kilometres
per hour) and an altitude record of 91,249 feet (27,813
meters). With supersonic flight in hand, the next frontier in
jet-engine progress called for engines of very great power,
suitable for aircraft of the largest possible size. The key
concept proved to be the "turbofan," also called the "fanjet."

General layout of a turbofan engine. Note that a separate
set of turbines drives the front fan, as in a turboprop. The
term "high-bypass" means that most of the air in the exhaust
comes from the fan and flows past the rest of the engine,
rather than flowing through it.
The "jet" of a jet engine is the hot stream of exhaust that
blasts out the back to produce thrust. However, that exhaust
carries power as well as thrust, which the turbines use to run
the compressor. By using a larger set of turbines, it is
possible to tap off still more of this power. The big turbine
then turns a fan, which somewhat resembles an airplane
propeller but has many long blades set closely together. The
fan adds its thrust to that of the jet. This arrangement
yielded the turbofan. It more than doubled the thrust of
earlier engines. It also further improved fuel economy. In
addition, turbofan engines were relatively quiet, in contrast
to earlier jets that produced loud shrieks and screams. GE and
Pratt & Whitney both built turbofans after 1965, with
Rolls-Royce, offering versions of its own. All truly large
airliners have used them, starting with the Boeing 747. These
engines have also powered large U.S. Air Force cargo planes,
including the C-5A and C-17.
The first aircraft to use these large engines was the Lockheed
C-5, which entered development in 1965 and first flew in 1968.
A key to its design was the engine—the GE TF-39 turbofan. It
had a dual-spool layout as well as a variable stator, with its
big fan providing 85 percent of the thrust. The dual-spool
arrangement gave the fan its own turbine for power, separate
from the rest of the engine. The compressor had 16 stages, or
rows of blades.
These three design principles—dual-spool layout, variable
stators, and the turbofan—remain in use to this day. All three
can even appear in the same engine, as with the TF-39. The
dual-spool design gives high thrust with good fuel economy.
Variable stators allow efficient operation at all flight
speeds. The big forward fan reduces noise, further improves
fuel economy, and produces much of the thrust. In turn, the
thrust of engines continues to increase. Germany's engine for
the wartime Me 262, the Jumo 004, delivered 2,000 pounds
(8,900 Newtons) of thrust. The J-57 was rated at 13,500 pounds
(60,000 Newtons) of thrust. The J-57 was similar in thrust but
weighed considerably less, which made it much speedier. Early
turbofans, around 1970, came in around 40,000 pounds (180,000
Newtons) of thrust. But GE's new GE 90 turbofan is rated at
close to 90,000 pounds (400,000 Newtons) of thrust! That is
why today's planes fly fast and are very large.
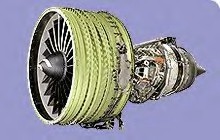
In the early 1990s, GE developed the GE90 turbofan engine to
power the large, twin-engine Boeing 777. The GE90 family, with
the baseline engine certified on the 777 in 1995, has produced
a world's record thrust of 110,300 pounds in ground testing,
has the world's largest fan at 123 inches in diameter,
composite fan blades, and the highest engine bypass ratio
(9:1) to produce the greatest propulsive efficiency of any
commercial transport engine.
In this engine, air is sucked in from the right by
the compressor. The compressor is basically a cone-shaped cylinder with
small fan blades attached in rows (eight rows of blades are represented
here). Assuming the light blue represents air at normal air pressure, then
as the air is forced through the compression stage its pressure rises
significantly. In some engines, the pressure of the air can rise by a
factor of 30. The high-pressure air produced by the compressor is shown in
dark blue.
|