
aircraft engine
history
Piston Engine development
Picture a tube or cylinder that holds a snugly fitting plug.
The plug is free to move back and forth within this tube,
pushed by pressure from hot gases. A rod is mounted to the
moving plug; it connects to a crankshaft, causing this shaft
to rotate rapidly. A propeller sits at the end of this shaft,
spinning within the air. Here, in outline, is the piston
engine, which powered all airplanes until the advent of jet
engines.
Pistons in cylinders first saw use in steam engines.
Scotland's James Watt crafted the first good ones during the
1770s. A century later, the German inventors Nicolaus Otto and
Gottlieb Daimler introduced gasoline as the fuel, burned
directly within the cylinders. Such motors powered the
earliest automobiles. They were lighter and more mobile than
steam engines, more reliable, and easier to start.
Some single-piston gasoline engines entered service, but for
use with airplanes, most such engines had a number of pistons,
each shuttling back and forth within its own cylinder. Each
piston also had a connecting rod, which pushed on a crank that
was part of a crankshaft. This crankshaft drove the propeller.
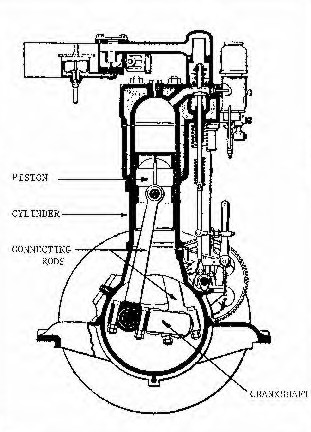
Cutaway view of a piston engine built by Germany's Gottlieb
Daimler. Though dating to the 19th century, the main features
of this motor appear in modern engines.
Engines built for airplanes had to produce plenty of power
while remaining light in weight. The first American
planebuilders—Wilbur and Orville Wright, Glenn Curtiss—used
motors that resembled those of automobiles. They were heavy
and complex because they used water-filled plumbing to stay
cool.
A
French engine of 1908, the "Gnome," introduced air cooling as
a way to eliminate the plumbing and lighten the weight. It was
known as a rotary engine. The Wright and Curtiss motors had
been mounted firmly in supports, with the shaft and propeller
spinning. Rotary engines reversed that, with the shaft being
held tightly—and the engine spinning! The propeller was
mounted to the rotating engine, which stayed cool by having
its cylinders whirl within the open air.
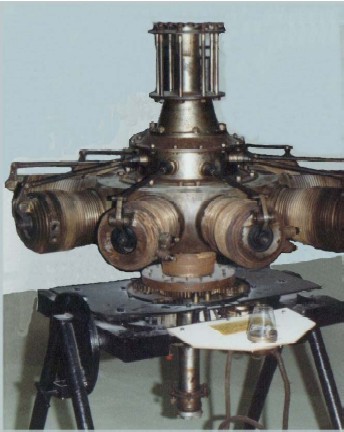
Numerous types of Gnome engines were designed and built, one
of the most famous being the 165-hp 9-N "Monosoupape" (one
valve). It was used during WWI primarily in the Nieuport 28.
The engine had one valve per cylinder. Having no intake
valves, its fuel mixture entered the cylinders through
circular holes or "ports" cut in the cylinder walls. The
propeller was bolted firmly to the engine and it, along with
the cylinders, turned as a single unit around a stationary
crankshaft rigidly mounted to the fuselage of the airplane.
The rotary engine used castor oil for lubrication.
During World War I, rotaries attained tremendous popularity.
They were less complex and easier to make than the
water-cooled type. They powered such outstanding fighter
planes as German's Fokker DR-1 and Britain's Sopwith Camel.
They used castor oil for lubrication because it did not
dissolve in gasoline. However, they tended to spray this oil
all over, making a smelly mess. Worse, they were limited in
power. The best of them reached 260 to 280 horsepower (190 to
210 kilowatts).
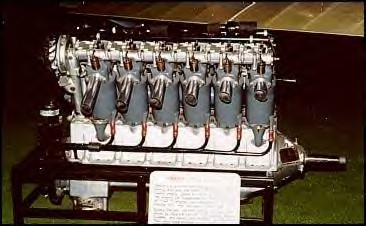
America's greatest technological contribution during WWI was
the Liberty 12-cylinder water-cooled engine. Rated at 410 hp.
,
it weighed only two pounds per horsepower, far surpassing
similar types of engines mass-produced by England, France,
Italy, and Germany at that time.
Thus, in 1917 a group of American engine builders returned to
water cooling as they sought a 400-horsepower (300-kilowatt)
engine. The engine that resulted, the Liberty, was the most
powerful aircraft engine of its day, with the U.S. auto
industry building more than 20,000 of them. Water-cooled
engines built in Europe also outperformed the air-cooled
rotaries, and lasted longer. With the war continuing until
late in 1918, the rotaries lost favor.
In this fashion, designers returned to water-cooled motors
that again were fixed in position. They stayed cool by having
water or antifreeze flow in channels through the engine to
carry away the heat. A radiator cooled the heated water. In
addition to offering plenty of power, such motors could be
completely enclosed within a streamlined housing, to reduce
drag and thus produce higher speeds in flight. Rolls Royce,
Great Britain's leading engine-builder, built only
water-cooled motors.
Air-cooled rotaries were largely out of the picture after
1920. Even so, air-cooled engines offered tempting advantages.
They dispensed with radiators that leaked, hoses that burst,
cooling jackets that corroded, and water pumps that failed.
Thus, the air-cooled "radial engine" emerged. This type of
air-cooled engine arranged its cylinders to extend radially
outward from its hub, like spokes of a wheel. The U.S. Navy
became an early supporter of radials, which offered
reliability along with light weight. This was an important
feature if planes were to take off successfully from an
aircraft carrier's flight deck.
With financial support from the Navy, two American firms,
Wright Aeronautical and Pratt & Whitney, began building
air-cooled radials. The Wright Whirlwind, in 1924, delivered
220 horsepower (164 kilowatts). A year later, the Pratt &
Whitney Wasp was tested at 410 horsepower (306 kilowatts).
Aircraft designers wanted to build planes that could fly at
high altitudes. High-flying planes could swoop down on their
enemies and also were harder to shoot down. Bombers and
passenger aircraft flying at high altitudes could fly faster
because air is thin at high altitudes and there is less drag
in the thinner air. These planes also could fly farther on a
tank of fuel.
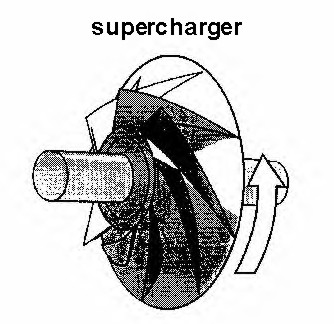
The supercharger,
spinning within a closely fitted housing (not shown), pumped
additional air into aircraft piston engines.
But because the air was thinner, aircraft engines produced
much less power. They needed air to operate, and they couldn't
produce power unless they had more air. Designers responded by
fitting the engine with a "supercharger." This was a pump that
took in air and compressed it. The extra air, fed into an
engine, enabled it to continue to put out full power even at
high altitude.
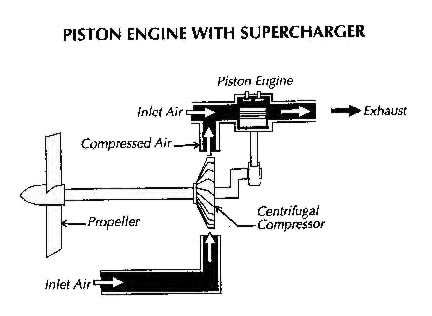
A supercharger needed power to operate. This power came from
the engine itself. The supercharger, also called a centrifugal
compressor,
drew air through an inlet. It compressed this air
and sent it into the engine. Similar compressors later found
use in early jet engines.
Early superchargers underwent tests before the end of World
War I, but they were heavy and offered little advantage. The
development of superchargers proved to be technically
demanding, but by 1930, the best British and American engines
installed such units routinely. In the United States,
the Army funded work on superchargers at another
engine-builder, General Electric. After 1935, engines fitted
with GE's superchargers gave full power at heights above
30,000 feet (9,000 meters).
Fuels for aviation also demanded attention. When engine
designers tried to build motors with greater power, they ran
into the problem of "knock." This had to do with the way fuel
burned within them. An airplane engine had a carburettor that
took in fuel and air, producing a highly flammable mixture of
gasoline vapour with air, which went into the cylinders.
There, this mix was supposed to burn very rapidly, but in a
controlled manner. Unfortunately, the mixture tended to
explode, which damaged engines. The motor then was said to
knock.
Poor-grade fuels avoided knock but produced little power. Soon
after World War I, an American chemist, Thomas Midgely,
determined that small quantities of a suitable chemical added
to high-grade gasoline might help it burn without knock. He
tried a number of additives and found that the best was
tetraethyl lead. The U.S. Army began experiments with leaded
aviation fuel as early as 1922; the Navy adopted it for its
carrier-based aircraft in 1926. Leaded gasoline became
standard as a high-test fuel, used widely in automobiles as
well as in aircraft.
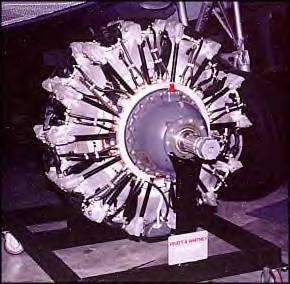
The Pratt and
Whitney R-1830 Twin Wasp engine was one of the most efficient
and reliable engines of the 1930s.
It was a "twin-row" engine. Twin-row engines powered the
warplanes of World War II.
Leaded gas improved an aircraft engine's performance by
enabling it to use a supercharger more effectively while using
less fuel. The results were spectacular. The best engine of
World War I, the Liberty, developed 400 horsepower (300
kilowatts). In World War II, Britain's Merlin engine was about
the same size—and put out 2,200 horsepower (1,640 kilowatts).
Samuel Heron, a long-time leader in the development of
aircraft engines and fuels, writes that "it is probably true
that about half the gain in power was due to fuel."
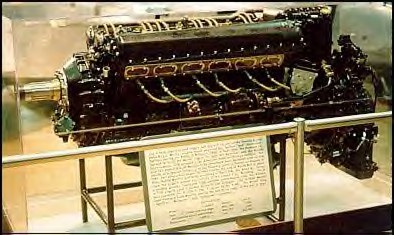
The V-1650 liquid-cooled engine was the U.S. version of the
famous British Rolls-Royce "Merlin" engine
which powered the "Spitfire" and "Hurricane" fighters during
the Battle of Britain in 1940.
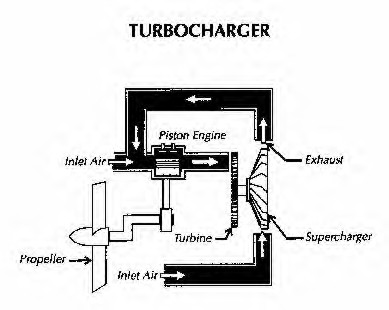
During World War II, the best piston engines used a
turbocharger. This was a supercharger that drew its power from
the engine' hot exhaust gases. This exhaust had plenty of
power, which otherwise would have gone to waste. A turbine
tapped this power and drove the supercharger. Similar turbines
later appeared in jet engines.
These advances in supercharging and knock-resistant fuels laid
the groundwork for the engines of World War II. In 1939, the
German test pilot Fritz Wendel flew a piston-powered fighter
to a speed record of 469 miles per hour (755 kilometres per
hour). U.S. bombers used superchargers to carry heavy bomb
loads at 34,000 feet (10,000 meters). They also achieved long
range, the B-29 bomber had the range to fly non-stop from
Miami to Seattle. Fighters routinely topped 400 miles per hour
(640 kilometers per hour). Airliners, led by the Lockheed
Constellation, showed that they could fly non-stop from coast
to coast.
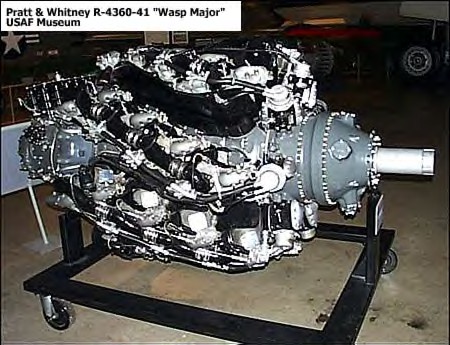
The Wasp Major engine was developed during World War II though
it only saw service late in the war
on some B-29 and B-50 aircraft and after the war. It
represented the most technically advanced and complex
reciprocating engine produced in large numbers in the United
States. I
t was a four-row engine, meaning it had four
circumferential rows of cylinders.
By 1945, the jet engine was drawing both attention and
excitement. Jet fighters came quickly to the forefront.
However, while early jet engines gave dramatic increases in
speed, they showed poor fuel economy. It took time before
engine builders learned to build jets that could sip fuel
rather than gulp it. Until that happened, the piston engine
retained its advantage for use in bombers and airliners, which
needed to be able to fly a great distance without refuelling.
Pratt & Whitney was the first to achieve high thrust with good
fuel economy. Its J-57 engine, which did these things, first
ran on a test stand in 1950. Eight such engines powered the
B-52, a jet bomber with intercontinental range that entered
service in 1954. Civilian versions of this engine powered the
Boeing 707 and Douglas DC-8, jet airliners that began carrying
passengers in 1958 and 1959, respectively. In this fashion,
jet engines conquered nearly the whole of aviation.
|