home
aero engines

Allison W3420s
Allison F-80 Trijet
Allison V-1710 Turbo-Compound
Clerget Rotary Engine
Curtiss Chieftain
Curtiss OX-5
Daimler-Benz DB 605
Gnome Monosoupape
Lycoming XR-7755
Macomber
Pratt & Whitney R-2800
Wright J-5 Whirlwind
Wright Cyclone
Wright Hispano-Suiza
|

Gnome
Monosoupape Type N Rotary
By Kimble D. McCutcheon
An air-cooled rotary that powered a number of
successful World War I aircraft
History
The rotary engine is unique in
that, unlike fixed radial engines, it has a
stationary crankshaft bolted to the firewall, with
everything else (cylinders, crankcase, propeller)
all rotating. The rotary in its original form is
extinct, with the term now being used to describe
"Wankel" rotary combustion engines such as
those built by Mazda. Though automotive and
motorcycle rotaries were built in the United
States and Australia in the 1890’s, the
design was developed for aircraft in Europe.
Laurent Seguin and his brother Louis, of the
Societe des Moteurs Gnome did this in France.
Their engine took the aviation world by storm when
displayed at the Paris Air Show of 1908. By 1917,
rotaries composed eighty percent of the engines
used in World War I (WWI). Originally introduced
as a 50-hp 7-cylinder engine, they developed
rapidly into 80 and 100 hp 9-cylinder engines. A
160 hp 14-cylinder held the world speed record
before WWI. The Gnome was widely licensed, and
copied in many forms by those clever enough
to get around Gnome patents.
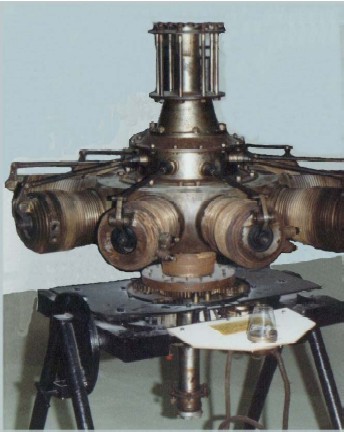
Figure 1. Gnome Monosoupape Rotary
One might ask how such an
evolutionary dead end as the rotary became such a
popular engine. Simply put, it was the right
engine for the time. Its primary advantages, low
weight, relatively low vibration, and reliability
(when properly maintained) allowed the creation of
many new aircraft designs. Early engines, running
on extremely poor gasoline, had low compression
ratios and turned very slowly. Propellers were not
advanced enough to allow more than about 1500 RPM.
At these slow speeds, most early engines vibrated
quite a lot. This was partially because of
unbalanced moving parts and partially because of
so few power pulses per revolution. A flywheel
could have been used to damp out the power
impulses, but would have added weight. Also,
engine cooling was poorly understood in
liquid-cooled engines and understood even worse in
air-cooled engines. So the genius of the rotary
was to reduce weight, provide a flywheel, make the
reciprocating parts move in circles instead of
straight lines (further reducing vibration), and
cool the engine, all with the same construction.
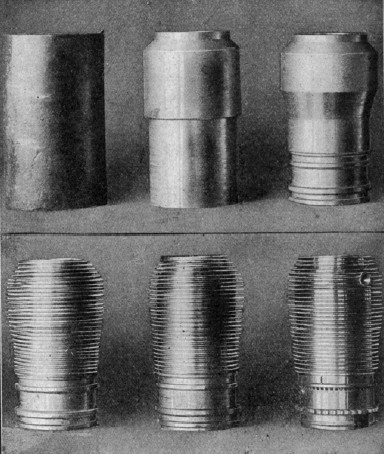
Figure 2. Cylinder Fabrication Sequence
Gnome engines were beautifully
constructed of polished steel, with many finely
machined cooling fins and tiny fasteners. They
were mostly built of forged steel machined to very
thin sections for lightness. Each cylinder, for
example, began life as a 97-pound nickelsteel bar.
When it was completed, it was only 1.5 mm thick
and weighed five and one-half pounds. Similarly,
the crankcase started as a 106 pound forging and
was reduced to a final weight of thirteen and
one-half pounds. Although this fabrication
technique is common in today’s aerospace industry,
it was quite unusual at the time.
Induction
Induction and exhaust in the
early Gnomes was interesting. There was no
carburettor or intake manifold. Air entered the
engine through the hollow crankshaft. A simple
needle valve, in combination with an air valve,
facilitated the pilot’s selection of the correct
fuel/air mixture. This along with lubricating oil
entered the crankcase, was thoroughly mixed by the
thrashing of internal parts, and distributed by
centrifugal force. On each intake stroke,
automatic intake valves in the crown of each
piston opened, admitting the mixture to the
combustion chamber. These valves were
counterbalanced to account for centrifugal force
and piston acceleration, with just the right
balance to allow the suction of the intake stroke
to open them. Once in the combustion chamber, the
mixture was compressed, ignited via a spark plug,
burned to produce a standard power stroke, and
finally exhausted directly to the atmosphere past
exhaust valves in the top of each cylinder. The
exhaust valves were operated by push rods and
controlled by a central cam ring.
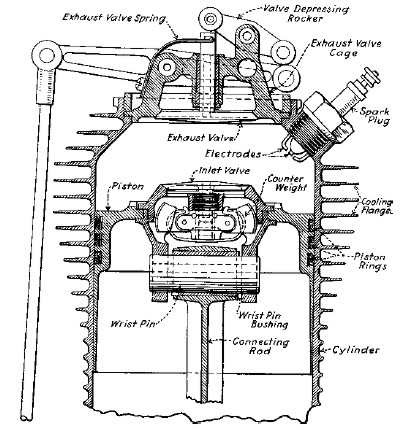
Figure 3. Early Cylinder and Valve Details
Since the crude fuel delivery
system had no provisions for throttling, most
rotaries ran at wide-open throttle all the time.
Slight variations in power were possible by
careful adjustment of the fuel/air mixture, and
this allowed formation flight. The aircraft
control stick was fitted with a "blip switch"
which served to momentarily shut off engine
ignition, making powered landings (and go-arounds)
possible. The automatic intake valves of the early
Gnomes turned out to be quite a headache for
maintenance personnel. In addition to presenting a
fundamental limit on engine speed and volumetric
efficiency, they got out of balance easily, gummed
up and got sticky, and worked poorly at higher
altitudes. Thus, they presented constant
maintenance problems, accounting in large part for
the extremely short time between overhauls (TBO).
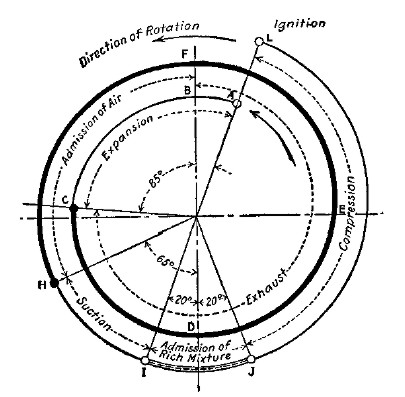
Figure 4. Monosoupape Induction Timing
The Seguin brothers, realizing
these problems, introduced the Gnome Monosoupape
(meaning single-valve) in late 1912. The automatic
intake valve was eliminated and a standard piston
substituted. This piston uncovered a ring of
intake ports at the bottom of its stroke. On the
exhaust stroke, the exhaust valve was opened early
to release pressure and reduce temperature in the
cylinder during the power stroke. When the piston
passed Bottom Dead Center (BDC), the pressure in
the cylinder and crankcase were hopefully equal
and the rich mixture in the crankcase hopefully
did not ignite. The exhaust port remained open for
the entire exhaust stroke and was left open past
Top Dead Centre (TDC) of the exhaust stroke until
about 90 degrees after TDC on the intake stroke
admitting fresh air to the cylinder. The exhaust
valve then closed, allowing the piston to create
suction in the cylinder and ultimately uncover the
intake ports at the bottom of the cylinder. The
very rich mixture in the crankcase was then
transferred into the cylinder via the uncovered
ports where it mixed with the fresh air and was
compressed. Although this technique eliminated the
troublesome automatic intake valves (and may have
contributed to perhaps doubling the TBO of the
engine), it further damaged the Gnome’s already
poor fuel consumption.
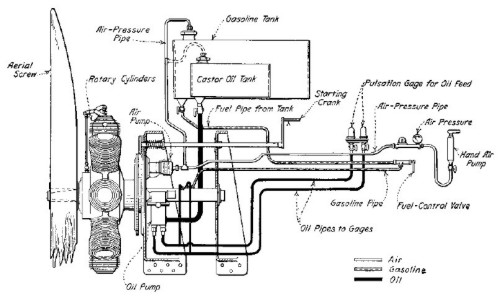
Figure 5. Rotary Installation and Plumbing
click on picture to see full size (opens in new
window)
Lubrication
Lubrication of the Gnome was
accomplished by injecting castor oil into the
fuel/air mix with a small pump. Castor oil was
used because it could not be easily dissolved into
the gasoline fuel, and because it possessed
lubrication qualities superior to mineral oils of
the day. The lubrication system was a total-loss
type, with over two gallons of castor oil being
sprayed into the air during each hour of engine
operation. This explains why most rotaries were
fitted with a three-quarters cowl ring, open at
the bottom. The cowl directed the spray of castor
oil, along with sparks from the exhaust, away from
the flammable airplane structure. In spite of
these attempts to deal with the excess lubricating
oil, pilots were still subject to, and in many
cases the victim of, the well-known laxative
qualities of castor oil. Many unscheduled stops
and off-airfield landings were credited to the
call of nature. Some pilots reportedly kept a
flask of blackberry brandy as an antidote to the
effects of the oil.
Service
The Gnome was, for its time,
light and reliable. Compared to liquid-cooled
engines of the day, it started easily, warmed up
rapidly, and allowed its pilot to become quickly
airborne to do his days bidding (We must not
forget the Gnome was in large part the prime-mover
of a weapons system). Due to the gyroscopic forces
of this rapidly rotating mass, aircraft handling
characteristics in a dogfight were strange. The
craft turned left instantly, but right very
reluctantly. In the hands of a skilled pilot, this
could be quite an advantage in combat. Starting
the engine was an adventure. It was turned over by
hand in a nearly flooded condition, and would
often catch fire due to the excess gasoline. The
fire would typically be confined to the cowl ring
and grass under the engine. The pilot would shut
off the gas and allow the engine to continue to
run on the excess as ground handlers hauled the
aircraft backward out of the fire. All would wait
for the fire to burn itself out. At just the right
moment, the pilot would re-open the fuel valve and
a successful start would have been achieved. When
the engine warmed up, the air valve was opened
wide and fuel re-adjusted to produce a correct
mixture. The engine was then run at full throttle
for the take-off, climb, and cruise, and landed
through the use of the "Blip switch", which was
used to temporarily ground out the ignition.
Though the Gnome was widely used and had a number
of advantages in its particular niche, it also had
a number of problems. It had a very high fuel
consumption so that the total weight of engine
plus fuel and oil placed it at a distinct
disadvantage for long flights. Its performance
fell off rapidly with altitude. Though reliable if
properly maintained, it was extremely
temperamental, requiring skilled mechanics to
overhaul it at typical intervals of 15-20 hours.
It was expensive, with a 70hp motor costing $4000
in 1912! Finally, its rotating mass limited its
size and consequently, its ultimate power. By the
end of the war, when tactics favoured a single
high-speed pass instead of the dogfight,
larger liquid-cooled engines prevailed and the
rotary was rapidly becoming an anachronism.
Specifications (Monosoupape Type
N, 1916)
Configuration: 9-cylinder
air-cooled rotary radial
Output: 160 hp @1,300 RPM
Weight: 330 lb
Displacement: 970 in
Bore x Stroke: 4.53" x 6.69"
Compression Ratio: 5.45:1
Mean Effective Pressure: 100.5 psi
Specific Weight: 2.06 lb/hp
Specific Output: 0.165 hp/in
Fuel Consumption: 29.1 gal/hr @
full power
Specific Fuel Consumption: 1.09
lb/hp/hr @ full power
Oil Consumption: 2.56 gal/hr @
full power
Specific Oil Consumption: 0.12
lb/hp/hr @ full power
6 hr mission specific weight: 1.55
lb/hp/hr (engine + fuel + oil)
|
|