
Harmon Rocket II
by Budd Davisson, courtesy of
www.airbum.com
The Name Says it All
It was a typical Arizona
morning in July, which is
to say, really hot. Most
folks were still having
breakfast, but as I
started the throttle
forward on the IO-540
Lycoming, I remembered
ATIS telling me it was 38°
C. That's over 100° in
real numbers which made
the density altitude right
at 5,000 feet. Welcome to
summer in the desert. This
would be not a fair
environment in which to do
an evaluation flight on
any airplane. The Lycoming
probably would be wheezing
to put out much more than
70%. Yeah, well tell that
to the Harmon Rocket. It
didn't seem to care. A
wheezer, it definitely was
not.
The
broad nose of the airplane
just barely covered the
runway ahead. In fact, a
little stretching would
have let me see over it,
but that was unnecessary
because the view around
the nose was so good. I
had an interesting
sensation as I brought the
power up: I felt as if I
had flown the airplane
many times before and
there was very little of
the usual first-flight
nervousness. It just felt
right, for some reason.
As the
power came up, the
airplane moved as quickly
as my hand did. Even
though runway lights were
starting to blur,
everything was so smooth
the frantic rush down the
runway was hardly
noticeable. In seconds I
raised the tail and in
another few was off the
ground.
I would
love to describe that
first take off in more
detail but can't. It
happened too quickly. In
subsequent takeoffs I
found the reason I can't
describe the first one is
that, besides the
incredible rush of the
runway flashing past,
there wasn't anything to
describe. The gear
geometry is nearly perfect
so even though there were
250 or more horses yanking
us down the runway, the
airplane tracked straight
with almost no rudder
inputs. When the tail was
up, the mains were stiff
enough that it was sending
no false signals and was
as stable as a billiard
table. The airplane
blasted (as in really
basted) straight down the
runway for only a few
seconds before we were off
the ground. The only thing
of note is a noticeable
tightening of the lip
muscles as the grin takes
over your face!
Sucking
the nose up to maintain
100 mph and leaving the
power in put the VSI
needle on the other side
of the 2,000 fpm mark. We
were at a density altitude
of 5,000 feet but still
showing 2,200 fpm! Now
that's performance. At sea
level, the airplane is
good for over 3,000 fpm.
On the
way out to the practice
area I brought the power
back to 25 square and
dropped the nose to 120
mph for more visibility.
At that speed and power
the climb dropped to a
paltry 1,400 fpm. I was
loving it!
I was
also loving the way the
cockpit felt. It's 32"
across at the front seat
and 25" in the back seat.
Since, from my perspective
up front I was flying a
single place airplane, I
didn't care how much room
the owner and builder,
Mark Frederick, had behind
me. All I knew was that I
was plenty comfortable and
having a good time. I was
also pleased to see how
well the controls were
placed in relation to the
seat. Everything felt just
about right.
It
became immediately
apparent the second the
gear left the ground that
the controls were actually
controlling the airplane
rather than, as with some
airplanes, just suggesting
a general direction. If I
moved my hand, the
airplane moved. It wasn't
until we were level in the
area, however, that I was
able to see exactly how
the controls reacted.
Since
the Harmon design started
life as an RV-4 it
exhibits all of the
wonderful handling
characteristics which have
made Van's airplanes such
stand-out winners. On all
axis, it has just enough
break-out force to ensure
the pilot will know where
neutral is, however, that
pressure is a little
lighter in pitch than in
roll. We were at half
tanks with two full sized
people onboard, so the CG
was aft in the envelope,
which Mark says changes
the pitch characteristics
dramatically. Even so, the
stick pressure climbed
with displacement
(positive gradient) just
as you'd expect it to. At
slow speeds, the pressures
get softer but the
pressure build-up is still
very normal feeling. The
only possible negative
might be that a low time
pilot flying the airplane,
with the CG aft, could
possibly get a PIO in
pitch going. The perceived
pitch sensitivity is as
much because of the
stick's short travel as it
is the reasonably light
pressures.
The
ailerons have slightly
more break-out force and
their pressures change
slightly with speed. More
speed, more pressure, and
vice versa. At no point
are they anything but
pleasantly light and the
control response is
immediate right down to
stall. Pressure the
ailerons and the airplane
moves. Push them hard and
the airplane leaps in that
direction.
I did a
series of aileron rolls
and the roll rate (this is
an educated guess) looks
to be 200°-220° per second
or more which puts it
close to aerobatic
specials like the S-2B
Pitts, but the pressures
are much lighter. One
weird characteristic I did
find is that as full
aileron deflection is
approached, there is a
noticeable "bump" in the
stick. I thought I had hit
Mark's leg, but he says
they all do that and the
accepted theory is that
the aileron tip is
stalling at full
deflection. What ever it
is, it didn't change the
rates.
The
Rocket has slightly
shorter wings than an RV
which puts the wing
loading up around 16.5
pounds/sq. foot, which
isn't terribly high, but
worth thinking about.
That's what was on my mind
as I brought the power
back and set up for a
clean stall. Again, the
airplane's RV heritage
showed through, as the
stall was preceded by
noticeable buffet and,
even when the stick was
held full back forcing it
deep into the stall, the
airplane was not trying to
do anything stupid. With
full flaps extended via
the willowy feeling flap
handle against the left
side of the seat, the
stall is much more abrupt
with a right roll. Here
too, however, it wasn't
anything unusual. Release
back pressure and you
could feel airflow
re-attach instantly. All
stalls were happening
under 60 mph with the full
flap version down around
54 mph.
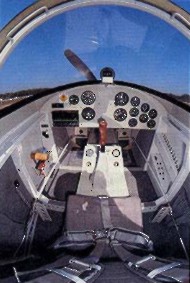
In
roll, if the airplane was
put in a bank, it would
stay there, so it was
fairly neutral in that
respect. In pitch, if the
nose was pulled 10 knots
off trim in cruise and
released, it would start
to return to the horizon,
but definitely wasn't in
any hurry to start back
down hill. With the CG
that far back in the
envelop, it was statically
positive, but just barely.
At slower speeds, it was
even weaker. As the nose
came down, however, it
over shot trim speed by
only 5 mph and it's
oscillations damped out in
less than two cycles.
Probably the biggest
criticism I had of the
airplane was that the trim
system was too sensitive
at cruise speeds. The tall
lever on the left fuselage
side took almost invisible
movements to get it
exactly where you want it.
Considering how stable it
is in pitch when trimmed,
it would be nice if the
trim travel at cruise was
a little longer and easier
to fine-tune. Mark
commented that in
approach, solo, it needs
all its trim and then some
and he hadn't figured out
how to change the ratio to
accomplish both
requirements. He said you
just get used to its
sensitivity in cruise.
We were
working in our local
aerobatic practice area
which has a ceiling of
8,000 feet. Flying my
Pitts in the same area, I
never even notice the
ceiling because I have to
work too hard to get that
high. In the Harmon, I was
constantly having to
remind myself to drop down
and stay below 8,000
because anytime the nose
was brought up, another
500 feet magically
appeared on the how-high
gage.
While
we were cruising around
showing about 190 mph (224
mph TAS) Mark commented
that side-by-side tests
with another airplane
showed his airspeed
indicator to be reading
quite low at cruise but he
flight plans 190 knots
(218 mph) and 11 gph. I
didn't think much about
that until later when I
realized those were lower
numbers than I'd been
hearing about on the
Rocket and asked him what
power settings he normally
used. He said he usually
only pulls 20" and 2300
rpm, which is down around
50% but that gets the fuel
flow down to around
10-10.5 gph at altitude.
At 55%, which is 21"/2400
rpm and 11.2 gph, he
figures 230 mph TAS at
10,000 feet.
The
most significant thing
about the airplane's speed
is that it is fast but the
gear is still hanging down
and it doesn't have cowl
flaps. On top of that,
Mark doesn't consider his
airplane even remotely
clean. What we have here
is speed with simplicity.
Some of the other Rockets
flying (18 are now
airborne with another 90
or so being built) which
have super-detailed
airframes and racing type
cooling and induction are
reporting cruise speeds in
excess of 250 mph!
Mark's
airplane is different than
most other Rocket's in
that it incorporates some
of the mods he has worked
out in his business of
supplying RV and Rocket
builders support
(Frederick Custom
Airframe, 512/365-8131, 80
County Rd #406, Taylor, TX
76574). He builds
components and provides
educational support for
any part of either
airplane as well as
selling several mods for
the Rocket. Besides his
fiberglass gear fairing
kits, he sells a canopy
kit which replaces the
flop-over single piece
bubble of the RV-4 with a
fixed windshield and
sliding canopy. He admits
that the fixed windshield
makes entry just a little
harder into the front pit
(it's hardly noticeable),
but the steel tube canopy
bow provides some
roll-over protection as
well as protecting his
face should he lose a
canopy. It also makes
taxiing with the canopy
open quite comfortable.
During
any part of the flight I
found dropping the nose
even the slightest amount
put the airspeed over 200
mph in a heart beat, so I
expected slowing down to
pattern speeds to be a
problem. Not so! In fact,
I was surprised to find it
to be "Cherokee normal" in
the pattern. It look
little more than bringing
the power back to 10-12"
to put it at 120-130 mph
on downwind and 14" to
keep it there. When that
big old Hartzell flattens
out, the airplane just
doesn't want to go
anywhere.
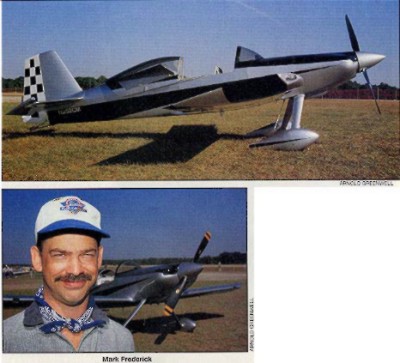
We flew what I consider to
be reasonably tight,
de-accelerating
Cherokee-like patterns,
with just a hint of power
to keep the engine from
cooling too much. 110 mph
on base down to 90 on
final with 85 mph over the
fence worked really well.
I noticed on one slightly
high approach that closing
the throttle completely
did add a lot of prop drag
and the rate of descent
went up, but it wasn't
anything heart stopping. A
loaded Cherokee or Yankee
with flaps comes down just
as quickly.
As I
started to flair and wiped
the power off, the
airplane just sat there,
solid as a concrete block,
while I tried to
approximate the
three-point attitude I'd
seen on takeoff. The first
landing was the best, as
the airplane plunked on
nice and even. I skipped
off the runway on another
one, the gear making a
resonating "proing" sound
as if scolding me.
However, no matter how
smooth the touch down was
or wasn't, as long as it
was straight on touch
down, it rolled perfectly
straight. I honestly don't
remember using any rudder
at all or, if I did, it
was so minor as to be
unnoticeable. This is
another place where the RV
heritage shows through.
The airplane has terrific
runway manners!! Also, in
landing mode, what little
pitch sensitivity there
is, isn't as noticeable.
I made
all landings without
flaps, as Mark said they
weren't really needed. I
also didn't try a wheel
landing, which Mark says
is, for some Rocket
pilots, the preferred
landing because they are
so easy. I doubt seriously
they could be easier than
the three-point landings.
You shouldn't be allowed
to log tailwheel time in
the airplane.
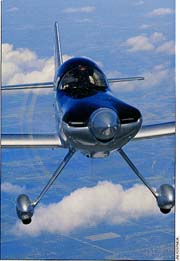
I
clearly remember climbing
out of the prototype RV-3
back in the early 1970's
at Fond du Lac and
thinking how far the
homebuilt airplane, as a
breed, had progressed. It
was, and still is, an
impressive airplane. Here
was a high performance
airplane, almost any pilot
could fly safely. Climbing
out of the Rocket, I felt
the same way. The Rocket
is a logical progression.
An
argument can be made that
there are RV's out there
with four-cylinder engines
that are as fast as some
Rockets. And there are.
However, make no mistake:
There is absolutely no
substitute for cubic
inches. None. When it
comes to all realms of
performance, including
going up, going fast, and
running at low power
settings, it's hard to
beat having more engine
than the airplane actually
needs. Is this a
subjective statement?
Absolutely! Is it true? In
this pilot's mind it is.
That's why it's
subjective.
When
you can run at well over
200 mph while pulling
barely 50% power at fuel
burns approximating
high-end four-cylinder
numbers, think what you're
doing for engine
reliability. You have the
power when you want it,
which gives the option of
not using it when its not
needed, like in cruise.
But, the cubic inches are
always there and they
always make themselves
known in the form of
increased performance.
Not
everyone needs a Rocket.
Some folks, however,
shouldn't live life
without one. You know who
you are.
Rocketizing the RV
John Harmon's Rocket II is
not without an element of
controversy: Quite
obviously it's a hot
rodded RV-4 and he makes
no bones about that fact.
In fact, he doesn't sell
kits for the airplane.
What he sells are parts to
convert an RV-4 to a
Rocket II. So, you buy an
RV-4 kit and replace
certain parts with
Harmon's kit as well as
rearranging and modifying
a few of the RV parts.
It's
easy to see why a possible
difficulty exists. No one
likes to see their product
modified into something
over which they have no
control. We contacted Dick
Van Grunsen at Van's RV
and his comment was,
"........"
The
bottom line seems to be,
if Van's doesn't know it's
for a Rocket, they'll sell
it.
Harmon
is dead honest about what
he's doing, in that he
continually says his
airplane is Van's airplane
but modified. In a
situation like this, it is
natural for a lot of
questions to arise
concerning how well the
modifications were
researched, how well are
the parts produced and how
serious is the producer?
Taking
the last question first,
John Harmon is very
serious. His business is
sheet metal fabrication
and building RV's became a
side-line to that business
in that he reached out and
put his arms around anyone
building an RV in his
area. As a businessman and
fabricator, he approached
doing the Rocket the same
as he would the rest of
his profession, which
provided the answer to
some of our questions. We
queried him specifically
about certain parts of the
airframe and how the
program was quantified.
He says
the wing of the Harmon
Rocket is a slightly
modified RV-4 unit. Harmon
wanted to make sure the
wing was strong enough to
handle the increase in
weight (empty went from
950 pounds to 1200
pounds). According to him,
to get it up to aerobatic
strength (6 G's) at
aerobatic weights required
clipping it 7 1/2" on each
side which cut the bending
moments down. Then the
ribs were re-pitched
closer together in the
centre section. He had the
wing professionally stress
analyzed by an engineer to
verify the strength and
the strength was
calculated on the spar
alone without taking the
skin into account. A
finished wing was
statically loaded to 6
"G's positive but no
negative loading was
attempted.
The
fuselage was widened in
the front seat and
lengthen 4" between the
two seats for more leg
room and to balance out
the heavier engine. The
fuselage uses several new
skins, ribs and frames and
is mostly Harmon parts
from the backseat forward.
The tail is unmodified RV.
The tail and the forward
fuselage were also
professionally analyzed.
The
longer-than-RV gear is
Harmon-machined from
titanium and is fitted
with bolt-on units to
mount Cessna-type axles.
It attaches to the new
motor mount in the same
manner as on an RV
The
normal parts acquisition
approach for a Rocket
builder appears to be a
phone call to Van's saying
"Send me a RV-4 kit
minus...." and the list of
Harmon supplied parts is
read off.
According to Harmon, he
has flown a flutter test
program in 5 mph IAS
increments from
approximately 150 mph to
300 mph.
|