Another reason the airplanes
aren't seen often is that we are
only now coming to the end of
the traditional three year
gestation period that begins
when the first kits of a new
design are delivered. Last year
there were no Rebels at Oshkosh.
This year there were seven.
Murphy expects as many as 100
may fly this year, so Oshkosh
could easily see the Rebel crowd
bursting at the seams next year.
Structurally,
the airplane is interesting for
a couple of reasons. In the
first place, it is a
professionally designed and
engineered unit. Second, it is
all aluminium and third, Murphy
has incorporated state of the
art CNC technology to make the
kits super easy to assemble.
Darryl Murphy
teamed up with ex-deHavilland
head of engineering Dick
Hiskocks when he decided to
build his idea of a bush bird.
Hiskocks was part of the
original design team on the
Beaver and a lot of that design
philosophy shows in the Rebel.
For one thing the fat 4415 wing
utilizes three spars and a bunch
of stringers for stiffness. On
top of that the fuel is kept in
wet sections of the wing and is
easily expandable from the basic
25 gallons to a whopping,
bladder busting 50 gallons for
those serious about staying up
there a while.
The fuselage
is a rounded box most notable
for its width, 44 inches across
the shoulders, which puts it in
C-182 category and 7 inches
wider than a C-152. It is the
width of the cockpit combined
with the small size of the
airplane that gives it a
deceivingly boxy look. It is
visually wide for its length.
The anti-canning creases seen on
the sides of the fuselage
replace the stiffeners of the
original design and save nearly
four pounds while eliminating a
bunch of parts and rivets.
And speaking
of rivets, that is one of many
areas where Murphy has worked
hard to reduce building time.
The airplane is specifically
designed around the Avdell Avex
blind rivet. Although appearing
to be of the common pop rivet
(actually a brand name) design,
the Avdels are universally
accepted in Europe and are
considered aircraft quality.
Although the mandrel is not
mechanically locked in place
like a Cherry or Huck MLS, their
aluminium shell is designed to
retain the mandrel as long as
practical. Because the aircraft
design takes into account their
lower strength (167 pounds in
shear versus 357 pounds for an
AN 4 in similar skin) there are
lots of rivets to be pulled,
nearly 20,000.
The real
beauty of the pulled rivet in
this application is that it
works with the Murphy's
pre-punched components to
eliminate the need for
traditional jigging. Other than
a 16 foot table that has to be
perfectly flat to act as a
datum, nothing needs to be
constructed other than the
airplane itself. Lots of
aluminium designs demand a
sizable time investment in jig
construction to ensure a
straight airplane. The Rebel,
however, depends on the flat
table and the accuracy of
factory-punched pilot holes to
jig the assemblies.
As the kit is
delivered, the skins have all
holes punched via CNC machines.
There is no bending of any
components to be done and
matching tooling holes are
located in individual pieces to
aid in positioning the skins.
The builder draws centrelines on
internal components such as
ribs, the centrelines are
positioned in the pre-punched
holes of the skins, and matching
holes drilled to size.
When
this type of tooling is combined
with the blind rivet, it is easy
to see why so many Rebels are
under construction and why so
many are about to be finished.
The skill levels usually
associated with jig construction
and traditional riveting are no
longer necessary. The learning
curve for this type of
construction would be almost
non-existent.
A builder
could, if desired, use bucked AN
rivets in place of the Avdels,
although the airplane would have
many more rivets than necessary
in that case. Also, there exists
the probability that AN 3
rivets, rather than -4s, could
be used in place of the 1/8"
Avdels because of the strength
is there and the weight would be
less. This is subject to final
engineering verification and
would undoubtedly increase
building time substantially
because the Avdels are so quick
to install.
Originally,
the Rebel had a "V" type bungee
gear but on the later kits they
ahve gone to an aluminum Wittman
type gear. This combined with
the sleeker cowl for the 160
engine upped the speed of the
airplane to a solid 125 mph in
cruise. More important,
according to factory test pilot
Rob Dyck (Jack, this is correct
spelling), it greatly improved
the airplane's ease of landing
and it rides rough fields much
more smoothly.
The airplane
is shipped in three basic kits,
the empennage ($xxx), the wing
($xxx) and the fuselage ($xxx).
If bought all at one time,. the
cost (fall 1994) would be $xxx.
The airplane
is approved for four engines and
the gross weight is changed
changed to match the engine. The
66 hp Rotax 582 is stickered at
1057 pounds (Canadian ultralight),
the Rotax 912 at 1450 lbs, the
0-235 Lycoming at 1650 pounds
and the 0-320 at XXXX pounds.
According to those at the
factory who have been keeping
track of customer's airplanes, a
912 airplane should empty at
about 600 and the 115 hp
Lycoming birds in the 825-875
pound range. The 160 hp version
they had at Oshkosh emptied at
950.
We poked
around in a builder's manual
and, although its hard to say
how good a manual is until you
actually try to use it, it
looked to be not only complete
but detailed in a very
commonsense sort of way. For
instance, in the tools required
to build each component they
listed a felt marker. One entire
step was spent waiting for the
epoxy chromate primer (supplied)
to dry because, if left tacky,
it would later catch and trap
drill filings. Nice touch!
Incidentally,
the way the parts are prepared
and the way the manual reads
instils confidence. This is not
always the case. Reading some
manuals leaves you overwhelmed.
My feeling after reading this
one was, "...even I could build
this airplane..."
Whether their
estimates of 500-600 hours to
build the basic airframe is
correct or not is hard to
verify, but given the methods
used in construction, the time
estimates may just be right.
I knew
absolutely none of the above,
when I scrambled into the
cockpit at the end of Runway 36
at Oshkosh. All I knew as I
scrambled into the right seat
was this was one of the very few
homebuilt aircraft I had boarded
that had seats adjusted via
Cessna type rails rather than
the stack-a-cushion system.
The door
latch, like so many parts of the
airplane was simple and to the
point: a spring loaded dog stuck
out the back edge and was
retracted by pulling on the
cable running through the middle
of the door. Very positive. Very
simple. Very light.
Settling back
in the seat and trying to orient
myself I noticed I felt I was a
long way back in the cockpit.
Rob Dyck explained from the left
seat that was the result of the
160 hp installation. They moved
the firewall back three inches
and the pilots almost twice that
amount. The result is the front
door pillars appear further
forward than normal and the
overhead cuts off some upward
vision. Even Rob said they
needed to open up the skylights
further. The headliner is a
pre-moulded piece that looked to
have plenty of room to install
bigger skylights which would do
wonders in opening up the
feeling of the cockpit and
increasing upward visibility.
Personally, I'd open up the
entire panel behind the main
carry-through back to the
stringer over the pilot's head.
If it needed more structure to
do that, it would be a
worthwhile investment.
What the
cockpit lacked in light, it more
than made up for in room. It was
much, much wider than it looked
from the outside. Further, as I
glanced around inside, I noticed
the third seat in back and asked
Rob about it. They designed the
airplane to handle 200 pounds in
the back seat and the real
fuselage has a floor so it can
be used as a camper. Rob said he
stretched out back there and
slept all the way back from a
fly-in while the other two kept
their eyes open.
It wasn't
until the airplane was running
that I noticed I had no brakes
on my side. Normally, not a big
deal, but as soon as I started
the turn onto the taxiway I
could tell the tailwheel springs
were too soft to get any
immediate response out of the
tailwheel. At a couple of points
i had to ask for some brake just
to make it around the corner.
Running the
MAC electric trim indicator into
the green, I kept an eye on the
flagperson standing at the edge
of the runway and immediately
powered up onto the centerline
at her request.
On the
runway, It was clear the
airplane had good visibility
over the nose. I couldn't see
straight ahead without
stretching just a little, but
the edges were clearly visible,
although the door pillar was
slightly in the way.
Cleared to
go, the throttle was gently
pushed forward, but from the way
the airplane reacted, you'd have
thought I hammered the throttle.
For what looked to be a normal
high wing airplane, this thing
rapidly assumed the personality
of a boxy bullet. As the
throttle found the panel I eased
the tail up and gently played
with the rudders. They were
effective, but the airplane
didn't really need much from me
to stay straight. More or less
straight anyway.
The tail was
barely off the ground when the
airplane launched and I ran into
the aforementioned climb
problem. There was no doubt in
my mind I could easily have had
3,000 feet at the other end of
the runway, the way that thing
was going up hill. Rob said it
was about 1,200 fpm, but at
70-75 mph that gave a deck angle
that approached ridiculous.
Without thinking, I throttled
back, as I pushed the nose over,
because my gut told me anything
with that kind of takeoff and
climb performance was going to
put its nose down and start
really hauling and I didn't want
that much speed in the pattern.
My gut was
wrong. With a 15% airfoil, it
wasn't about to accelerate
through Mach. It hit a drag wall
and hung in there at about 125
mph while I stuck my face in the
windshield looking around the
wing root for all the traffic I
knew was out there.
Once over the
lake, I let the nose up and we
went upstairs in a hurry.
We levelled
out and I started playing. As I
did Rob reached up to the
overhead lever and put the flaps
into a 6 degree reflexed
position which he says tacks a
few knots onto cruise.
I rammed some
aileron into it without rudder
to see how much adverse yaw it
had and was surprised to find it
had very little. I had expected
those Hershy bar wings to
require lots of correcting
rudder but they didn't. The
rudder was plenty effective, but
very little was needed for
coordination.
The ailerons
themselves are Cessna-normal.
Nothing out of the ordinary with
Spam can roll rates. In other
words, it doesn't have a quicker
than normal feel that many
homebuilts exhibit. Later,
during stalls with the ailerons
drooped, the roll response fell
off because of the drooping,
which is one of the reasons they
limit it to 18 degrees. Other
than the change with flaperons
out, the controls on all axis
will feel very familiar to
anyone flying the airplane
because they are right in the
middle of the profile. They feel
a little like every airplane but
exactly like none
With enough
altitude under us, I brought the
power back and crept up (or is
it down?) on a stall. Somewhere
around 45 mph it started
buffeting and the rate of
descent went up a few hundred
fpm and the stick was against
the stop. The flaperons made
very little difference in the
nose attitude or speed bleed-off
but they did knock at least four
mph off the stall. When totally
stalled and clean the ailerons
and rudder worked nicely and
easily controlled the airplane.
With the flaperons out, the
control was noticeably softer.
Given time I would have liked to
mess with very slow speed turns
or turning stalls and see if
large aileron inputs in those
situations would stall the
inside wing. Rob says they've
looked at that but haven't found
it to be a problem. Still, it
would be fun to investigate it.
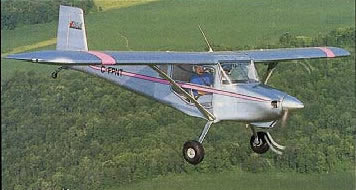
I poked and
prodded the airplane and found
the only thing I actually didn't
like about it was the visibility
and the general "dark" feeling
of the cockpit. A lot of older
airplanes (Pacer, Maul, Chief,
etc) are that way, but the Rebel
doesn't need to be. Larger
skylights would make a big
difference. Past that, there
isn't much that could be
changed.
We threaded
our way through traffic back to
Oshkosh and I did my best to get
the airplane slowed down to the
65 mph Rob wanted on final.
Unfortunately, we were forced
into flying a bastardized wide,
fast approach and I never really
had a chance to get it trimmed
up on speed.
That however
was no excuse for the lousy
landing I made.
I'm here to
tell you the spring gear on the
airplane really works well. Even
though I touched down harder
than necessary with a little
drift to the left, the airplane
didn't hop, jump or try to bite
either its own tail or mine.
After touchdown I did, however,
find I would have given anything
for a set of brakes or much
tighter tailwheel springs.
Between the two of us, Rob and I
put on quite a show. If I had
done a better job on short final
all the gyrations wouldn't have
been necessary, since even
though I gave it every
opportunity, it never did
anything particularly spooky.
Just embarrassing.
The ground
handling, had I done my part and
had the tailwheel been a little
more responsive, was actually
not much more difficult than a
Citabria. I think!. The
forgoing, the pilot and the
tailwheel springs, made it
appear more difficult than it
was.
During the
entire approach at no time did
the nose get in the way. It
wasn't until just before
touchdown (such as it was) I was
even aware the nose was out
there.
The Murphy
Rebel and its apparent success
says something really important
about sport aviation and the
markets it represents. At the
very least it says there is a
market out there for a really
usable airplane that has a
little character all its own. It
says there are a lot of people
who want airplanes that are
practical in the ways they
personally define that word.
They don't need 200 mph or
aerobatics or any of the other
flash and glitz that is so much
a part of some designs. They
aren't looking for Shelby
Cobras, they are looking for
four-door Chevies they can drive
and drive and drive. That's the
Murphy Rebel. Its an airplane
for the masses. Its an airplane
to be used, not simply owned.
Maybe that's
why its named the Rebel. It is
going against the current trend,
marching to its own
four-cylinder dummer and all
that.
The Rebel is
a usable airplane and that's
saying a lot.